You Should Know These 8 Plastic Trends
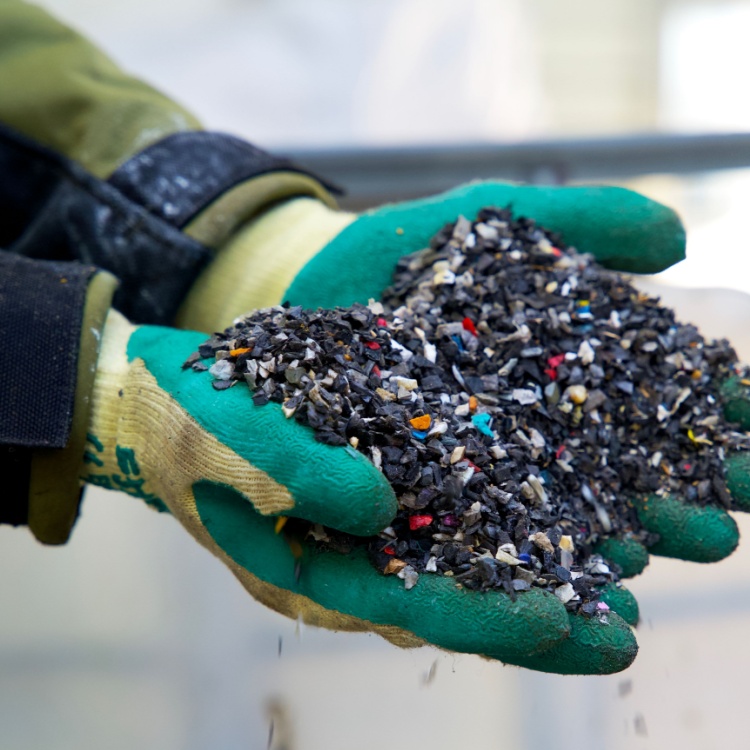
Plastics have transformed various businesses due to their flexible applications, long-lasting nature, and cost-effectiveness. Currently, the plastics industry is evolving, emphasizing the creation of eco-friendly approaches, advancements in recycling technology, and the adoption of circular economy approaches.
Plastic manufacturing companies play a crucial role in the global economy, innovating products and generating employment. What used to be a US$522-billion revenue global industry in 2020 is projected to expand at a CAGR of almost 4% by 2028.
However, the production of plastic has caused substantial environmental harm, with millions of tons of waste polluting oceans and landfills annually. For the industry and the environment to move towards sustainability, the sector must adopt innovative solutions.
As we progress toward a greener future, it's essential to identify the pivotal trends and breakthroughs influencing the expansion of plastic manufacturing. This article examines some of the noteworthy advancements now taking place within the plastics sector.
Top 8 trends in plastic manufacturing
The industrial market is rapidly evolving, with new industrial solutions driving innovation in plastic manufacturing. Here are the top 8 trends shaping the future of the industry:
-
Eco-friendly practices
Sustainability measures are becoming integral to plastic manufacturing, focusing on reducing environmental impact and promoting eco-friendly practices throughout the production process. A McKinsey survey revealed that 91% of plastics manufacturers are either currently adopting or planning to adopt eco-friendly practices in their operations.
-
The growing popularity of bioplastics
Unlike conventional petroleum-based plastics, bioplastics come from renewable sources like sugarcane, corn flour, algae, plants, or waste products. These materials may break down naturally, making them suitable for composting and capable of lessening environmental impact. Biodegradable additives, including cellulose and oil-based materials, further enhance their ability to decompose.
-
Promoting recycling initiatives
Many plastics producers are setting up recycling initiatives for their waste and working to boost overall plastic recycling rates. These actions help reduce waste and
emissions and conserve valuable resources. Additionally, extended producer responsibility (EPR) is gaining popularity, holding manufacturers accountable for every stage of their product's lifecycle, including disposal and recycling.
-
Adopting a circular economy model
A circular economy model focuses on reducing, reusing, and recycling plastics to reduce waste and enhance resource efficiency. It involves designing products with their end-of-life in mind and setting up effective recycling systems.
-
Advocacy and educational efforts
A good number of plastic manufacturers are supporting advocacies and public awareness programs that highlight sustainability and environmental care. There is an increasing acknowledgment in industrial manufacturing, particularly the plastics industry, that environmental sustainability is crucial not only for the planet but also for long-term business viability. Consequently, more companies are taking measures to lessen their carbon footprint.
-
Improving and developing recycling innovations
Conventional plastic recycling methods frequently encounter challenges due to the diverse compositions of plastics, contamination issues, and significant energy demands. Nonetheless, researchers and innovators are working on advanced recycling technologies to address these obstacles.
For example, chemical recycling is an emerging technique that decomposes plastic waste into its basic molecular components, enabling the creation of new plastics with characteristics similar to those of original materials.
-
Experimenting with lightweight plastics
According to Grand View Research, the global market for lightweight materials in the automotive market, where plastics play a key role, was estimated at $76.6 billion in 2020. It is projected to expand at a CAGR of 7.6% by 2028. Lightweighting involves efforts by manufacturers to decrease the weight of plastic products while maintaining performance and quality.
This trend is motivated by the need to lower material use, transportation expenses, and environmental impact. One method to achieve lightweighting is through careful material selection, with these plastic materials available to create lighter products:
- Polycarbonate (PC)
- Polyethylene (PE)
- Acrylonitrile butadiene styrene (ABS)
-
Smart factories
PwC reports that 91% of plastics manufacturers are investing in Industry 4.0 technologies, including smart factories that utilize real-time data to enhance production efficiency. By 2025, the global market for these plastic manufacturing technologies is projected to reach $4.5 billion.
Digitally integrated factories have machines and interfaces capable of real-time communication. Facilitated by technological innovations like the Internet of Things (IoT) and artificial intelligence (AI), these interconnected factories offer the following benefits:
- Enhanced efficiency and output
- Data-driven decisions
- Better quality control
- Energy efficiency
-
Increased automation and personalization
In the plastics manufacturing industry, automation and customization are closely linked trends. Innovations in digital technologies and automation now enable manufacturers to create highly customized products on a large scale, all while cutting costs and boosting efficiency.
Automation, which is the use of robots, machines, and digital tools, is progressively being applied to plastic manufacturing processes such as packaging, molding, and quality assurance.
Meanwhile, customization involves creating products adapted to individual customer requirements or preferences, such as specific colors, shapes, scales, and other characteristics. Tech advancement has enabled manufacturers to deliver more personalized products while maintaining efficiency and affordability.
-
Innovative molding techniques
Significant progress has been achieved in plastic fabrication molding methods. A key result of these developments is the creation of more adaptable and durable products from PVC and polycarbonate, meeting diverse industry requirements. These materials now provide outstanding strength and flexibility for various applications.
Additionally, advanced molding techniques have facilitated the creation of detailed and complex designs. These innovations also enhance the quality and accuracy of the final products. As a result, overall performance and functionality are improved, guaranteeing that the final products meet top-quality standards.
-
Plastic fabrication breakthroughs
These novel manufacturing methods are transforming the application of widely used plastics in crucial sectors like healthcare. Advanced fabrication methods have enabled the development of highly tailored and precise medical instruments and apparatus. Furthermore, these advancements have led to the creation of sterilizable and biocompatible plastics for essential medical uses, enhancing patient care standards and supporting more accurate diagnoses and effective treatments.
-
Near-shoring
Near-shoring is a trend that entails moving manufacturing sites closer to the end markets they cater to. The primary factors driving this trend in the plastics industry include:
- Greater supply chain reliability
- Reduced transportation expenses
- Shorter lead times
- Better quality management
- Greater adaptability
These plastic manufacturing trends underscore the growing demand for innovative, lightweight materials in the automotive industry. As manufacturers continue to prioritize fuel efficiency and sustainability, the use of advanced plastics is expected to expand, driving further growth and evolution in the sector.As one of the Top 20 EMS companies in the world, IMI has over 40 years of experience in providing electronics manufacturing and technology solutions.
We are ready to support your business on a global scale.
Our proven technical expertise, worldwide reach, and vast experience in high-growth and emerging markets make us the ideal global manufacturing solutions partner.
Let's work together to build our future today.
Other Blog
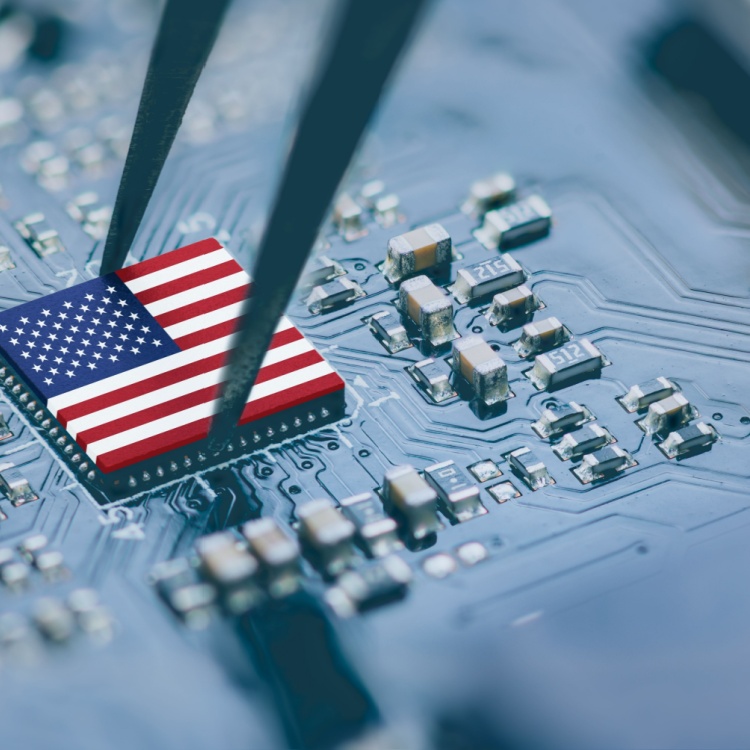
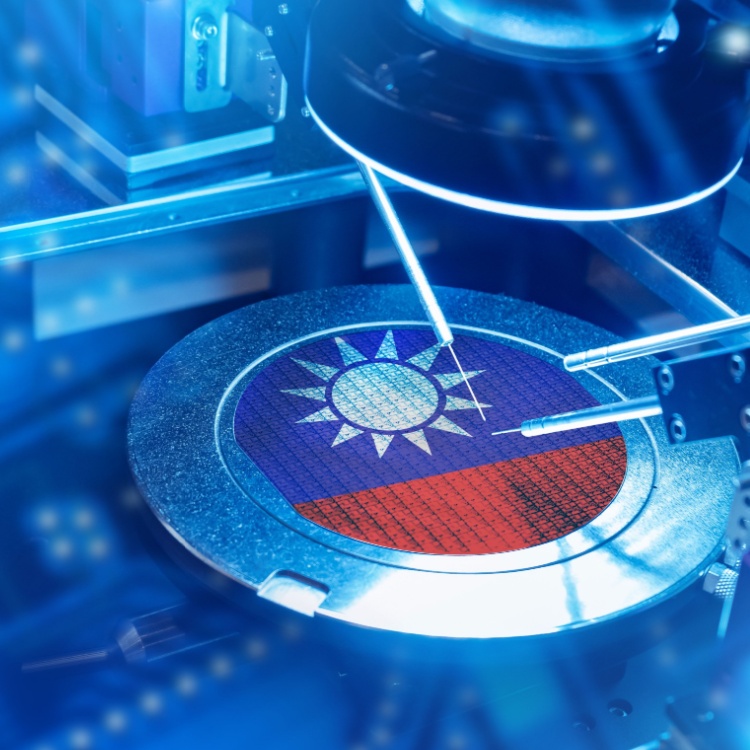
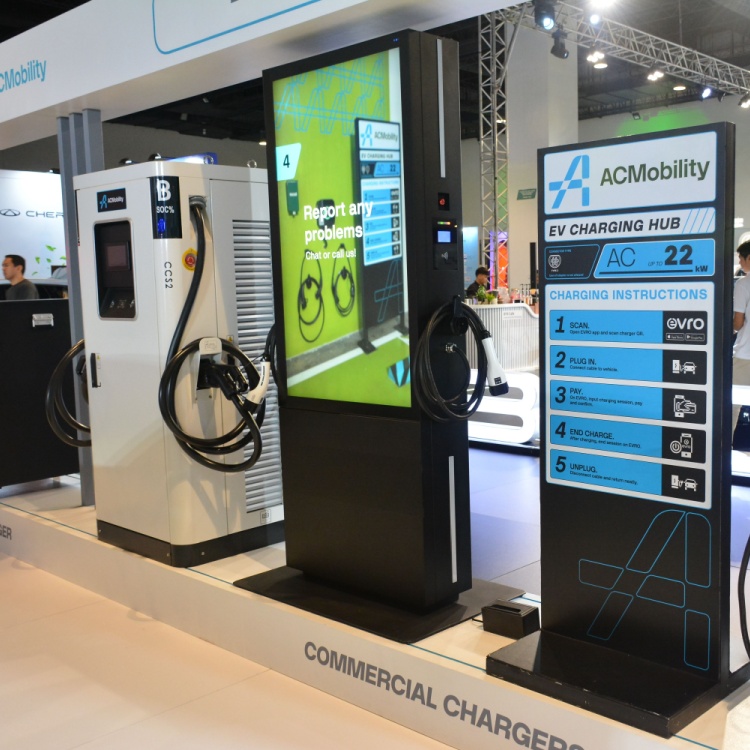