Why You Should Adopt AR and VR
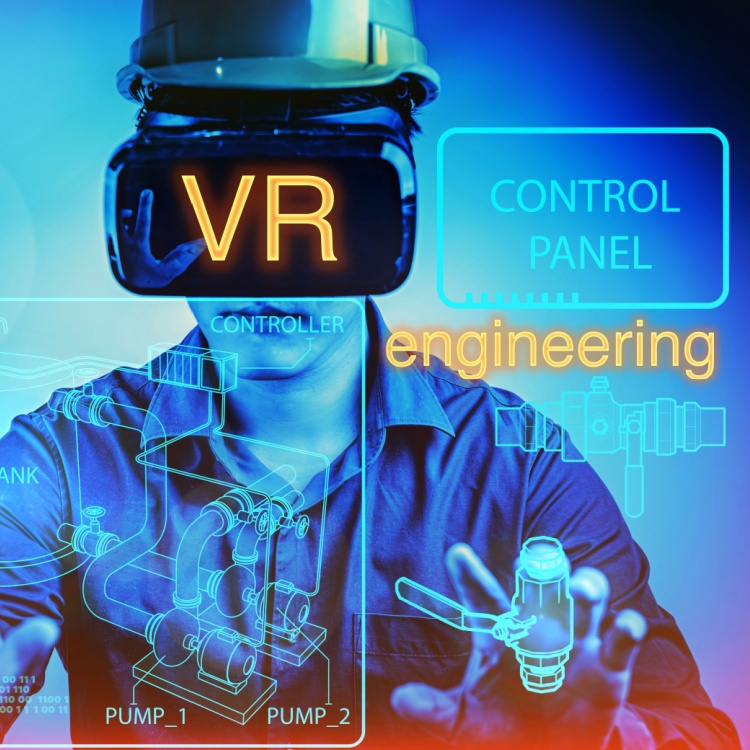
Most investments in immersive technologies have focused on gaming, with healthcare also adopting augmented reality (AR) for surgeries and patient information. In education, AR enhances lectures with interactive elements. Now, immersive engineering is making significant strides in global manufacturing.
Immersive engineering uses cutting-edge technologies like augmented reality (AR), virtual reality (VR), and mixed reality (MR) to deliver interactive and engaging experiences.
AR overlays digital information onto the real world, VR surrounds users in a fully simulated environment, and MR blends real and virtual worlds to interact with digital elements in real time.
These technologies allow users to view, immerse in, and modify digital objects and spaces in ways that traditional 2D screens cannot achieve.
A major use of immersive engineering in manufacturing is digital twins—virtual representations of physical equipment, operations, or workflows for testing and evaluation. These replicas enable manufacturers to track real-time performance, anticipate maintenance needs, and enhance operations. Interacting with digital twins through immersive technologies offers engineers a more detailed understanding and supports better decision-making.
How immersive engineering boosts manufacturing
According to this latest news in the manufacturing industry, expenditure on industrial metaverse (IMV) solutions and services is expected to increase by 22.8%, reaching $6.3 billion by 2030, as immersive and collaborative features become central to Industry 4.0 software development.
IMV has become an integral component of industrial manufacturing solutions by leveraging immersive technologies and digital twin projects. This combines data modeling, AI-driven simulations, enterprise systems, and external information sources to connect digital twins with other systems. Currently, the primary IMV applications focus on training, fostering teamwork, and operational scheduling, emphasizing solutions that deliver rapid, positive business outcomes.
In manufacturing engineering, AR and VR replicate the production setting. This lets design and engineering teams create prototypes and assess machinery and processes in a virtual environment before implementation. Factory workers can access simulations of essential manufacturing and assembly operations using a VR headset or a specialized application.
7 benefits of immersive engineering in manufacturing
As VR becomes more widely adopted, it will continue to overcome limitations and push the limits across various industries through cutting-edge and engaging technologies.
-
Training and skill development
Immersive engineering simulations provide practical training scenarios, allowing workers to enhance their skills safely. For instance, VR can simulate an assembly line, improving skills and reducing errors. By transferring training for complex machinery and procedures to VR, the risk of mistakes with actual equipment is minimized.
-
Improved product design for manufacturing
Engineers use VR and AR to visualize, test, and modify product designs in a virtual environment, enhancing design for manufacturing. This method helps detect and correct issues early, significantly cutting down the time and cost of developing physical prototypes.
-
Streamlined operations and maintenance
Immersive engineering tools facilitate remote monitoring and real-time guidance for maintenance tasks, which helps improve operational efficiency. By reducing downtime and ensuring that equipment runs at peak performance, these tools enhance overall productivity and reliability, leading to more efficient operations and lower maintenance costs.
-
Increased collaboration
Virtual environments facilitate collaboration among teams across different locations, allowing for seamless communication and problem-solving in real-time, which accelerates decision-making processes.
-
Better quality control
Immersive technology allows for more precise inspections and quality assessments, leading to higher standards in product quality and reducing the likelihood of defects.
-
Cost reduction
Immersive engineering saves manufacturing costs by reducing the need for physical prototypes, minimizing travel expenses for collaboration, and cutting downtime.
-
Customization and flexibility
Immersive tools allow manufacturers to quickly adapt to changing demands by simulating and implementing new processes, leading to a more agile and responsive production environment.
Siemens’ key partnerships driving the expansion of immersive engineering
Immersive engineering is well-suited for manufacturing because it enables full factory experiences in virtual environments. It supports future integration and marketplace opportunities, similar to the approach Siemens has taken with their partnerships.
Siemens and Detecon
Siemens Xcelerator, in partnership with Detecon, facilitates real-time decision-making and quality standards. Detecon’s intelligent quality controls, robust cybersecurity, and proactive maintenance ensure smooth digital manufacturing. The Digital Process Twin optimizes manufacturing by simulating real data, improving efficiency from research and development to production.
Meanwhile, Siemens’ NX Immersive Explorer software enhances immersive engineering by letting users explore design models in a fully immersive environment before physical prototyping. Users can interact with and view designs in true scale, manipulate parts, and assess designs from various angles and scenarios. Features like accurate measurements, annotations, and snapshots improve design reviews and communication.
Siemens and Evesoft
Evosoft’s factory simulation services, integrated within the Siemens Xcelerator portfolio, enable manufacturers to verify and enhance their processes. By delivering rapid, customized simulations of models of facilities, equipment, and workflows, manufacturers gain performance insights that support strategic and operational decisions. This ensures optimized processes and efficient resource utilization.
Siemens and BAE Systems
Siemens and BAE Systems have entered a five-year partnership to create a roadmap for advancing emerging engineering and production capabilities. This collaboration expands on Siemens’ NX software for product engineering and Teamcenter for Product Lifecycle Management.
The agreement also includes edge computing technologies and the validation of innovations. Siemens and BAE Systems aim to accelerate benefits in environmental responsibility, industrial digitization, and supply chain advancement, both regionally and internationally. This partnership, rooted in shared goals, enhances technology adaptation and promotes manufacturing solutions.
Siemens and Sony
Siemens and Sony are collaborating to integrate the Siemens Xcelerator software with Sony’s XR head-mounted display, the SRH-S1. Developed with Siemens' NX software, this display highlights their synergy. Siemens Xcelerator, featuring NX Immersive Designer, blends physical and virtual environments with accurate 3D interaction. Sony’s SRH-S1 enhances this experience with controls tailored for engineering, making the IMV more intuitive.In conclusion, immersive engineering has the potential to revolutionize global manufacturing by seamlessly integrating cutting-edge technology with human expertise. This approach not only enhances productivity and precision but also fosters innovation, creating a more sustainable and resilient manufacturing landscape.
As one of the Top 20 EMS companies in the world, IMI has over 40 years of experience in providing electronics manufacturing and technology solutions.
We are ready to support your business on a global scale.
Our proven technical expertise, worldwide reach, and vast experience in high-growth and emerging markets make us the ideal global manufacturing solutions partner.
Let's work together to build our future today.
Other Blog
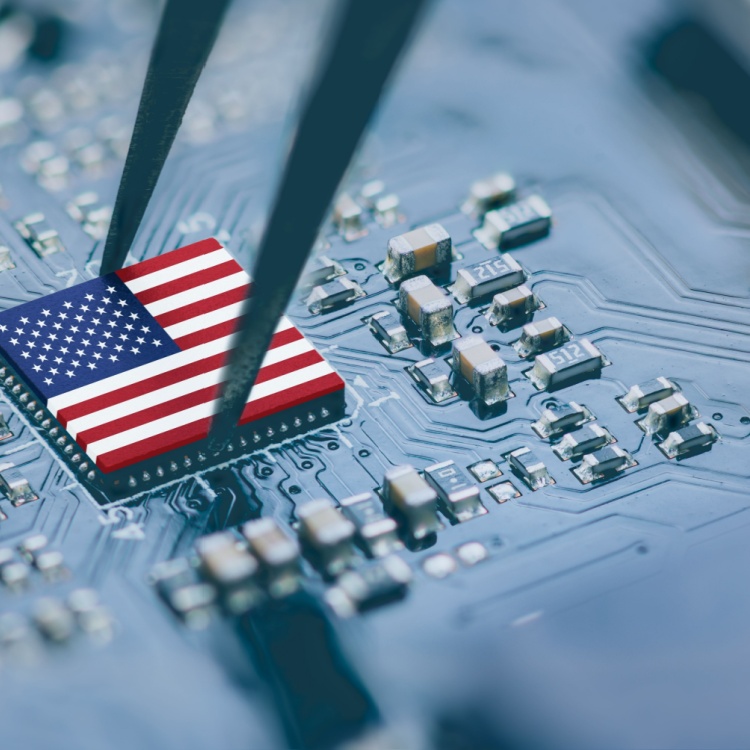
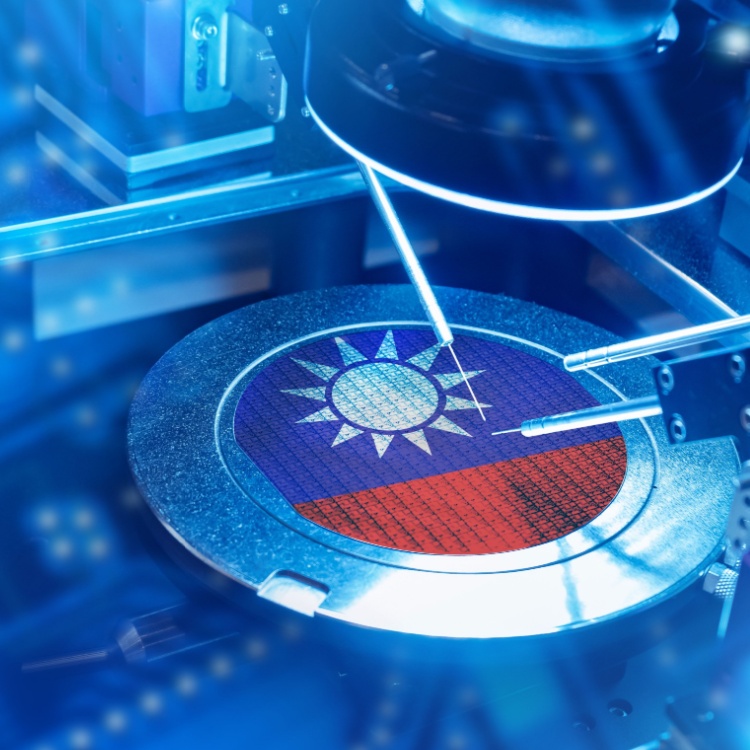
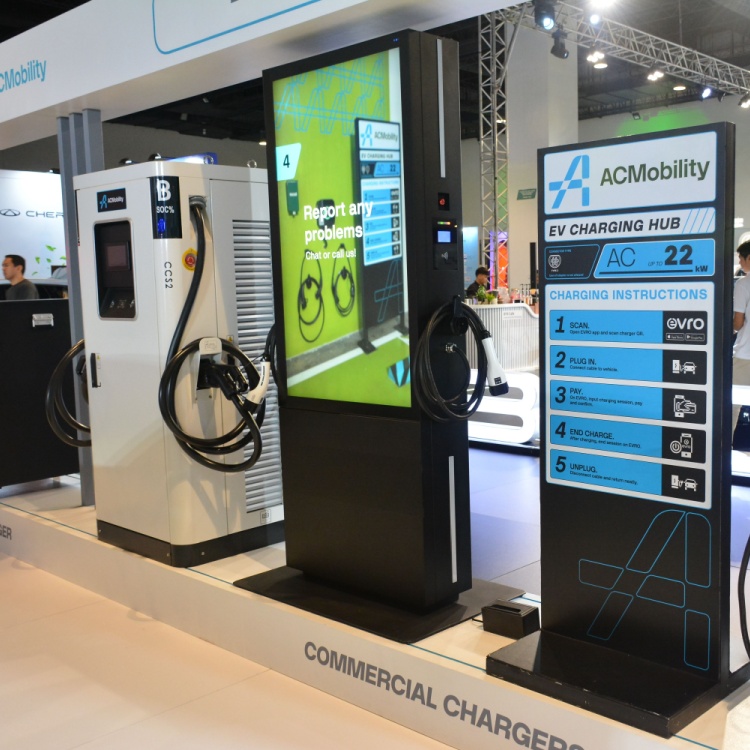