Top 8 EMS Supply Chain Challenges
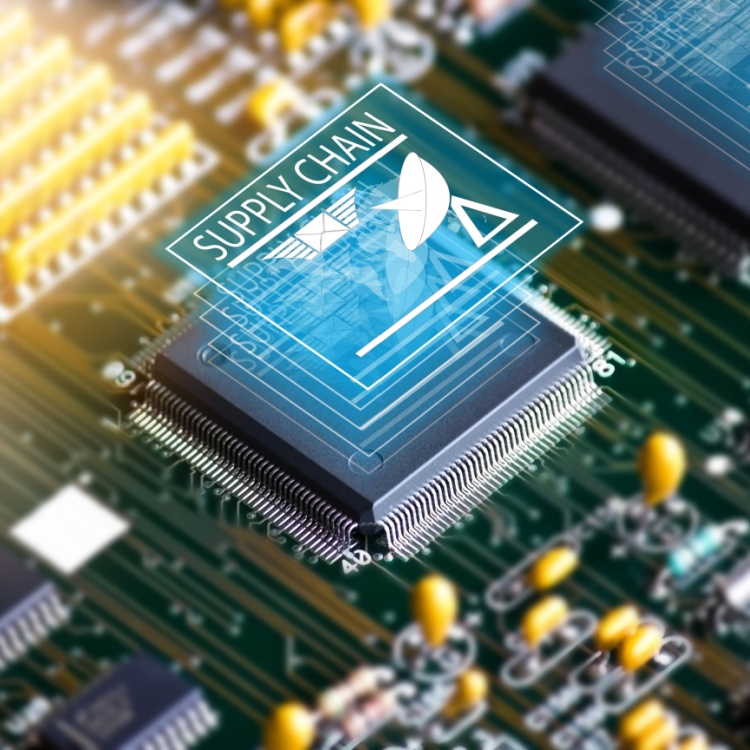
The Electronics Manufacturing Services (EMS) industry is key in turning electronic designs into finished products. A robust supply chain is essential to improve operational efficiency, delivery times, and cost efficiency. However, this complex system faces challenges. We explore these issues and offer manufacturing solutions to keep the industry running smoothly.
Electronic manufacturing companies can’t seem to shake off supply chain issues since COVID-19. But despite the constant presence of challenges, experts predict that the market for global electronics components will expand to over US$328 billion by 2031, a 76% increase from the 2022 figure.
Meanwhile, McKinsey reports that the electric automotive market, particularly those that involve self-driving capabilities, will boost demand for vehicle microchips until 2030, making up 89% of the total automotive semiconductor market in the same year.
Despite this positive outlook, figures can change if supply chain problems persist and worsen. To get a better picture of how EMS can be future-ready and ensure excellence on the global manufacturing stage, we examine its current difficulties and possible solutions in its logistics network.
Top 8 supply chain challenges of the EMS industry
We look at the most pressing challenges that significantly impact the industry’s manufacturing capabilities.
-
Soaring supply prices
Inflation has surged globally, impacting countries with the highest rates seen in decades. As raw material costs rise, elevated interest rates limit borrowing for businesses. This may involve prepaying for goods, extending credit lines, or downsizing products. Increased shipping surcharges and transport expenses are expected, prompting enterprises to explore alternatives like freight consolidators. As inflation persists, understanding its effects and adapting strategies will be essential for sustaining growth.
-
Technological advancement
Digital evolution, which includes artificial intelligence (AI) and the Internet of Things (IoT) presents both advantages and challenges for logistics management. Technologies that encourage the rise of electric vehicles, automation, and immediate delivery services have the potential to revolutionize industrial solutions. However, integrating these advanced systems with existing supply chain operations can be complex. While they aim to enhance efficiency and reduce costs down the road, successful implementation is crucial for achieving desired outcomes.
-
Inconsistent market demand
A lack of comprehensive historical data to forecast demand remains a significant hurdle for retailers in predicting market needs. Consumers are shifting their spending priorities amid a broader economic downturn following the pandemic, coupled with the rapid and often unpredictable trend cycles driven by social media platforms. Achieving success in e-commerce requires extensive research, data interpretation, and in-depth insights into the target market.
-
Supply shortages and delivery delays
The explosive growth in sectors such as 5G technology, and artificial and virtual reality (AR and VR) is generating an unprecedented demand for better supplier quality and electronic components. This surge has led to significant shortages of critical components like chips and capacitors for power module assembly, which disrupt production schedules across various industries. Moreover, backlogs at suppliers have extended lead times from weeks to several months, complicating inventory management and production planning for EMS companies. These challenges not only hinder assembly workflows but also impede the timely delivery of finished products, impacting customer satisfaction and market competitiveness.
-
Compliance challenges
Overcoming regional regulatory challenges poses significant challenges for EMS manufacturers. To ensure product compliance with safety protocols and emission guidelines in different markets, manufacturers must engage in meticulous tracking and testing processes. This involves not only meeting the initial regulatory requirements but also adapting to changes as laws evolve. Manufacturers must invest in training and resources to stay informed about these shifts, which impact production timelines and overall business strategy.
Conflicts over tariffs, international embargoes, and export restrictions are major factors that severely hamper global supply chains. For instance, the trade conflict between the US and China has escalated costs for EMS manufacturers depending on Chinese-sourced parts. Embargoes imposed on specific countries can lead to shortages of critical materials, while export restrictions limit access to advanced technologies. These disruptions make it difficult for companies to plan their operations and inventory efficiently. As global tensions rise, particularly with instability in Eastern Europe, the Middle East, and the conflict between China and Taiwan, the free and predictable movement of goods across borders becomes increasingly uncertain and challenging.
-
Quality control and stability
Ensuring uniform product quality across a disjointed global logistics network, with numerous production locations, presents a significant challenge for EMS manufacturers. A defect in any component from one supplier can have a cascading effect, disrupting production across multiple facilities and potentially leading to widespread issues. To safeguard their brand reputation and avoid the financial burden of costly recalls, EMS manufacturers must establish and enforce stringent quality control protocols. This includes conducting thorough testing at every stage of the production process to catch defects early and minimize the risk of disruptions. Such measures are crucial for maintaining high standards in a complex, interconnected supply chain.
-
Sustainability and environmental issues
With increasing environmental awareness, EMS manufacturers are under growing pressure to adopt sustainable practices. These practices include incorporating renewable energy in their production processes, minimizing waste, responsibly recycling electronic waste, and sourcing eco-friendly components. While the renewable energy market offers significant opportunities for enhancing sustainability efforts, the high costs of implementing greener processes remain a considerable barrier. Despite the potential long-term benefits—such as reduced operational expenses and an enhanced brand reputation—many manufacturers struggle to invest in the necessary infrastructure and technologies for a more sustainable operation.
Possible solutions
Supply chain management seems like a huge task, but with proactive steps, EMS companies can maximize their capital and stay resilient. Here are some viable options:Overcoming supply chain challenges in the EMS sector requires a multifaceted approach that embraces innovation, collaboration, and strategic planning. Ultimately, building a robust supply chain is not just a necessity; it is a key driver of long-term success in the competitive EMS landscape.
As one of the Top 20 EMS companies in the world, IMI has over 40 years of experience in providing electronics manufacturing and technology solutions.
We are ready to support your business on a global scale.
Our proven technical expertise, worldwide reach, and vast experience in high-growth and emerging markets make us the ideal global manufacturing solutions partner.
Let's work together to build our future today.
Other Blog
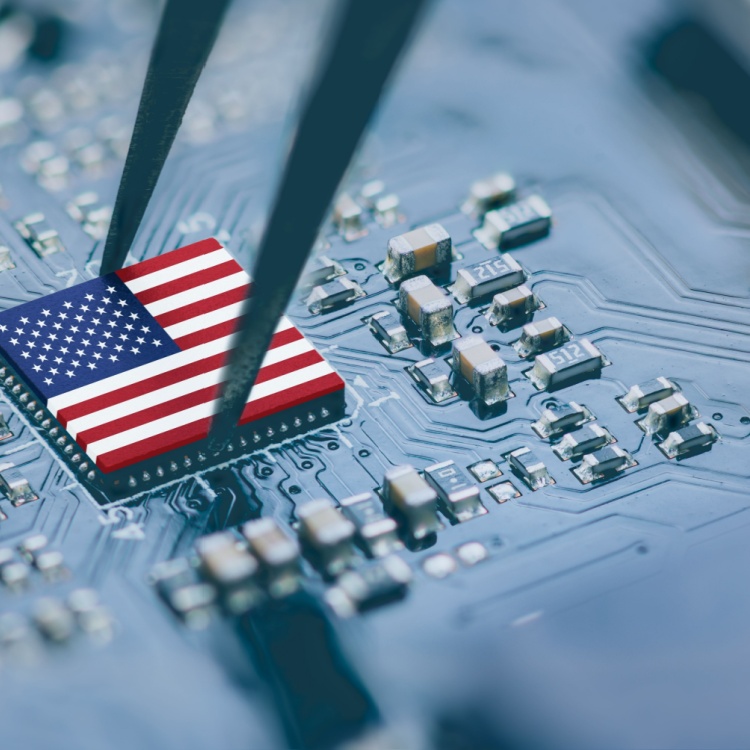
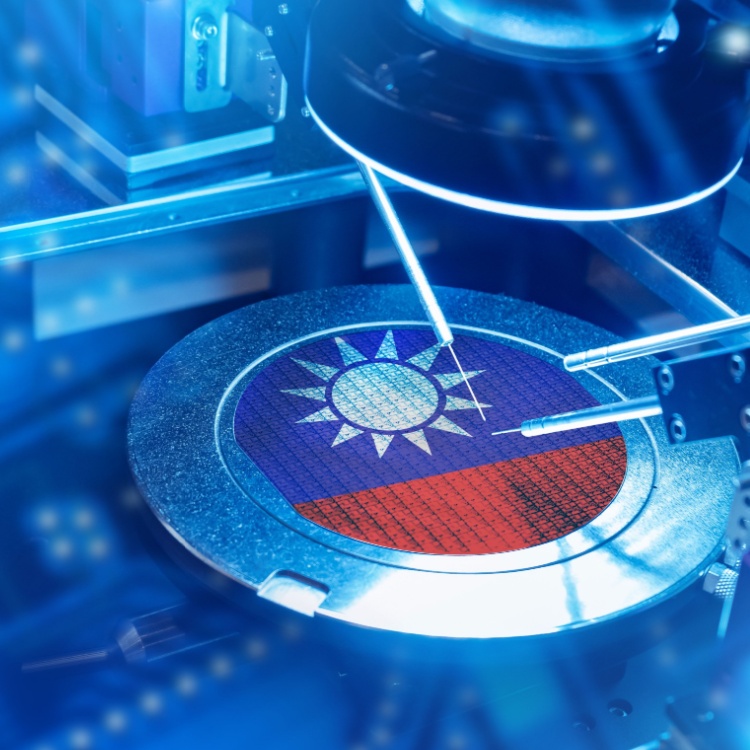
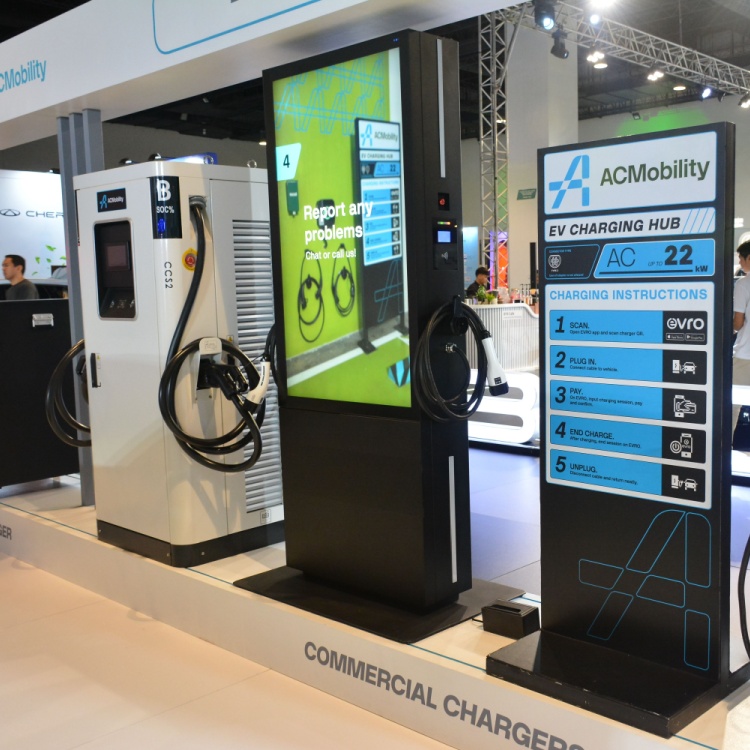