Technology to Future-Proof Supply Chains
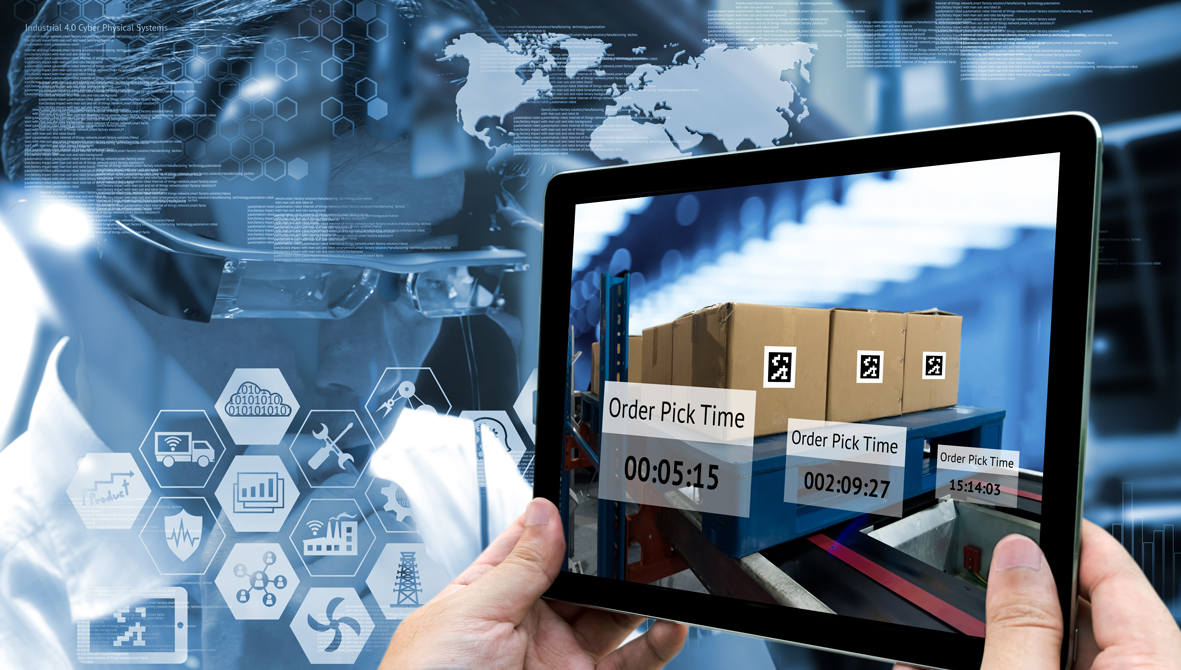
Disruptions caused by the COVID-19 pandemic make a strong case for reshaping supply chains in our interconnected global economy. How can business leaders build supply chain resilience to mitigate risks from future threats and disruptions?
It is known as “the world’s factory”—a chief manufacturer of high-value products and components. It is also one of the largest consumer markets in the world. Clearly, China is an economic powerhouse that is vital to many global value chains.
More than 200 of the Fortune Global 500 firms have a presence in the sprawling, highly industrialized city of Wuhan, where the then-outbreak began. Home to the country’s largest inland port, Wuhan is an industrial and transportation hub for central China. When this city of eleven million people closed its doors to contain the virus, economies and industries all over the world felt the impact.
Most are feeling it still. The world’s economy has never been more interconnected, and months of border closures, nationwide lockdowns, travel bans, and factory closures caused by the COVID-19 pandemic have affected global trade at an unprecedented speed and level.
As a global electronics manufacturing and technology solutions company, IMI has 22 manufacturing plants in 10 countries and is one of the Top 20 EMS companies in the world. It provides services to industry leaders in the global automotive, industrial, aerospace, and other markets.
“We have about 20,000 employees globally,” Arthur Tan, CEO of IMI, shared during an interview with EMSNow last June. “Keeping them safe and managed during this pandemic is definitely a challenge, with each policy of each government we have to adhere to. And on top of that, how to address the supply chains from the rest of the world is also a challenge.”
“The countries are entering and exiting the COVID-19 pandemic in different cycles,” Tan continued. “When you’re working and producing globally, the supply chain is actually interconnected.”
With five manufacturing plants in the country, China is IMI’s second-largest footprint. “When China first entered [the COVID-19 pandemic cycle], it affected quite a bit of manufacturing globally. For particular components, China produces 60-80% of the world’s total supply,” Tan explained. “But when China came out of the cycle, the United States and Mexico started going in, so it’s a trickle effect. It limits us from being able to source from specific countries. And when you start closing borders, you can’t move goods. As long as we have these cycles propagating through different markets, your supply chain will be affected.”
The pandemic has caused severe disruptions in supply chain processes, from sourcing and production to procurement and logistics. These stoppages and slowdowns have underscored the need for businesses to reconfigure their supply chains not only for cost competitiveness but for risk competitiveness as well. Moving forward, how can companies make their supply chain more efficient and resilient to better manage supply risk and disruption?
The way forward: visibility and digitalization
The World Economic Forum, together with global management consulting firm Kearney, recently consulted with more than 400 senior executives in operations and supply chain management from different industry sectors. In this white paper, they list five key imperatives to ensure the long-term success of manufacturing and supply systems:
- Rapid tailoring of manufacturing and supply systems to changing consumer behavior
- Agile manufacturing and supply system set-ups enabled by advanced technology
- Logistics coordination across and within global value chains
- Adoption of new ways of working and governing to increase manufacturing resilience
- Shared responsibility and collaboration among companies and authorities to address social and environmental challenges

“Enhanced supply-chain management and adoption of digitalization has never been more important,” shares Anne Petterd, a Partner in Technology, Communications and Commercial team at Baker McKenzie. “Companies with well-considered supply-chain risk management processes will be better-placed to identify the impact of disruptive events on their supply-chain and product-offering, providing them with an opportunity to assess how to best respond in tough circumstances.”
Investing in advanced manufacturing technologies will allow companies to have end-to-end supply chain visibility, utilize data to support decisions and predictions, increase production agility, and leverage automated processes. Through digital technology and analytics, companies can unravel the complexities of supply chains, anticipate disruptions, and quickly develop an appropriate response.
Let’s take a look at some of these technologies.
Cognitive supply chain
IBM describes cognitive technology as “radically disruptive systems that understand unstructured data, reason to form hypotheses, learn from experience and interact with humans naturally.” Bringing together advanced artificial intelligence (AI), cognitive computing, and cloud technology, a cognitive supply chain will be automated and self-learning. It will be able to perceive, predict, plan, and act based on real-time supply chain data and transactions—information that is crucial to averting potentially disastrous situations like, for example, a food crisis.
Scenario planning
Foresight is key to preparation, and scenario planning allows organizations to establish action plans that can be deployed rapidly. Employing analytics to forecast disruptions and their impacts can greatly enhance risk management practices. Simulations can be run to identify an optimum point between conflicting objectives. Enabled by artificial intelligence (AI) and automation, simulations can help propose and not only predict. By examining past events and hypothesizing future threats, organizations will be able to “identify strategic and concentrated supplies that are at risk, and most importantly, recognize when current internal risk capacities prove insufficient,” says professional service network KPMG.
Blockchain
From paper copies of packing lists to a bill of lading (a detailed list of a shipment of goods), trade and supply chains are heavy on the paperwork—which is labor-intensive and vulnerable to human error. Companies can have greater visibility, efficiency, and auditability in their supply chains through blockchain technology. It can replace slow, manual processes and save on costs in procurement, provenance and traceability, digital payments and contracts, logistics, and manufacturing.
Last May, the Digital Container Shipping Association (DCSA), a non-profit group composed of container shipping companies from all over the world, launched a collaborative effort to push for an electronic bill of lading (eBL), citing research that the container shipping industry could potentially save 4 billion US dollars a year if 50% adoption of eBL is achieved. Several international associations in the maritime shipping industry are also calling for the digitalization of port communities all over the world.
The supply chain of tomorrow
As the global health crisis continues, business leaders will be focused on the now and the next. But focusing on the beyond is just as important—no matter how confusing or overwhelming that may be.
“At IMI, we believe there are opportunities in a crisis,” shares Tan. “From experience, we know that as an organization, especially in the EMS space, we need to be able to transform quickly when needed. And this capability has been set up in deep layers within our structure as part of our risk management.”
“We hope to be able to use this time to refocus and reassess IMI’s position in the manufacturing space,” Tan continues. “Shifts in our focus as well as our move towards digitization will be among the things we have in mind as we recover and pivot this year.”
Adopting new technologies means adopting a new mindset—nurturing a business culture that is open to change and sees challenges as opportunities. Companies and leaders who do so will be enabled by technology, powered by data, and driven by insight, making their supply chain of tomorrow will be smart, agile, and better equipped to face future disruptions.
Other Blog
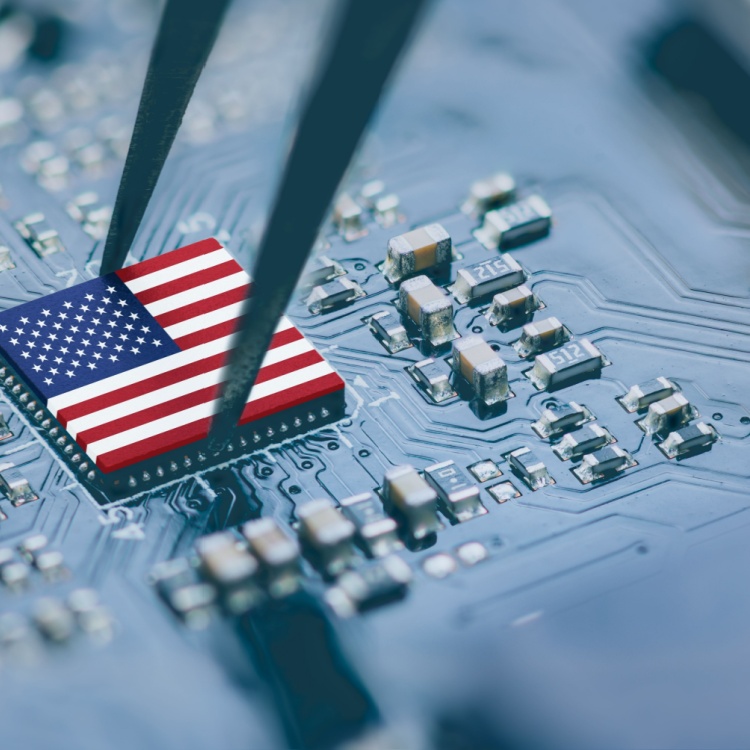
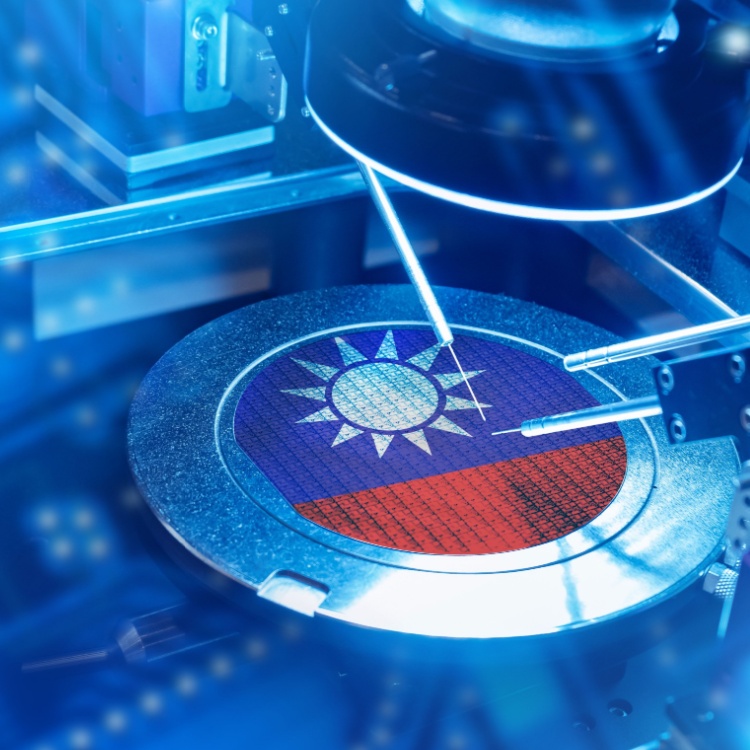
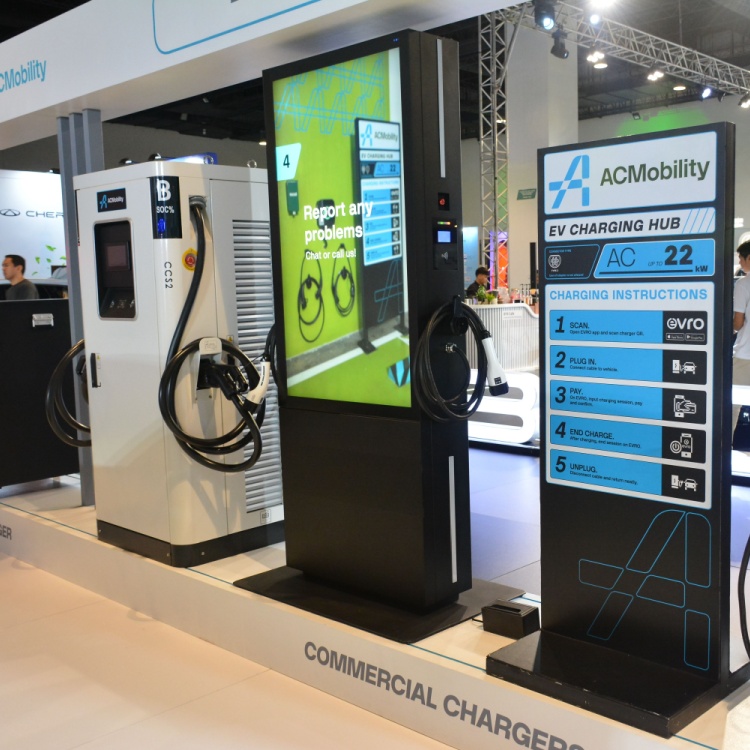