The Process of Plastic Manufacturing
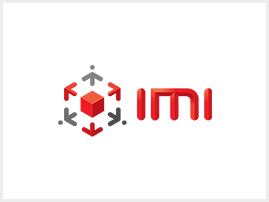
June 28,2019,Philippines—Although global manufacturing providers have started making their manufacturing solutions and processes more eco-friendly, plastics are still abundantly used in the industry because of the longevity and durability they offer at an affordable cost. From product components to packaging materials, plastics can be found anywhere in our everyday lives. Fortunately, several efforts to make plastic manufacturing more sustainable are now underway as well.
That said, plastics come in thousands of varieties with different specific base properties, derivatives, and additives that are formulated to cover a wide range of functions. It also has two main categories; thermoplastics which are plastics that can easily be shaped every time it is heated and cooled, and thermosets which are plastics that remain in a permanent solid state after manufacturing.
Of course, this means that there are various methods used to process different kinds of plastics. Used accordingly to the purpose of the plastic to be manufactured, each plastic manufacturing method has its advantages and disadvantages.
Injection Molding
One of the most common plastic manufacturing methods, injection molding is suitable for high-volume mass production with consistent quality. It works by melting plastic resins inside the injection machine and then drives the melted plastic into a metal mold to produce a plastic part or product with complex shapes.
Injection molding is predominantly used for thermoplastics because of its flexible characteristics, although some thermosets can also be processed through it.
Extrusion Molding
Similar to injection molding, extrusion molding machine also melts plastic before shaping it. However, rather than putting the melted plastic into a mold, it is pressed and forced out of a 2D opening or die in the shape of the desired finished product instead.
If injection molding is suitable for the production of 3D objects, extrusion molding, on the other hand, is suitable for creating long hollowed products such as pipes, tubes, and cables.
Blow Molding
There are several variations of blow molding including injection and extrusion blow molding, but in general, the essential process of blow molding works by inflating a hollow pre-made thermoplastic parison or tube inside a mold by use of air pressure until it forms into the desired shape.
This type of plastic manufacturing method is often used by manufacturers for the creation of plastic bottles and other containers.
Rotational Molding
Rotational molding or “rotomolding” is another plastic manufacturing method suitable for creating hollow objects. Different from blow molding, however, rotomolding is a process that involves heating a hollow mold filled with powdered thermoplastic inside a furnace while being rotated around two axes to allow the powdered plastic to coat the entire interior of the mold. This is suitable for the production of larger hollow objects such as auto parts and furniture.
Compression Molding
Most commonly used for thermoset plastics, compression molding can be easily understood by comparing it to the process of making waffles. Using heat and pressure, plastic is created by putting the thermoset material into an open, heated mold cavity which will be enclosed by a top mold or plug in order to squeeze or compress the plastic into its desired shape.
3D Printing
The global manufacturing industry has been increasingly utilizing 3D printing into its manufacturing solutions, and that includes the plastic manufacturing sector. 3D printing creates plastic by building material layer by layer following a computer-aided design (CAD) model.
The process differs depending on the 3D printing technology used, but generally, they are slower and more-labor-intensive than other plastic manufacturing processes, making them not so suitable for mass production. Hopefully, 3D printing technologies will continue to improve and allow larger volume productions in the future.
Almost every EMS Company in the Philippines and other countries around the world offer diverse plastic manufacturing solutions. There is no need to worry about creating more waste, though, since the industry has been doing continuously making their manufacturing solutions more and more sustainable than before.
Other Blog
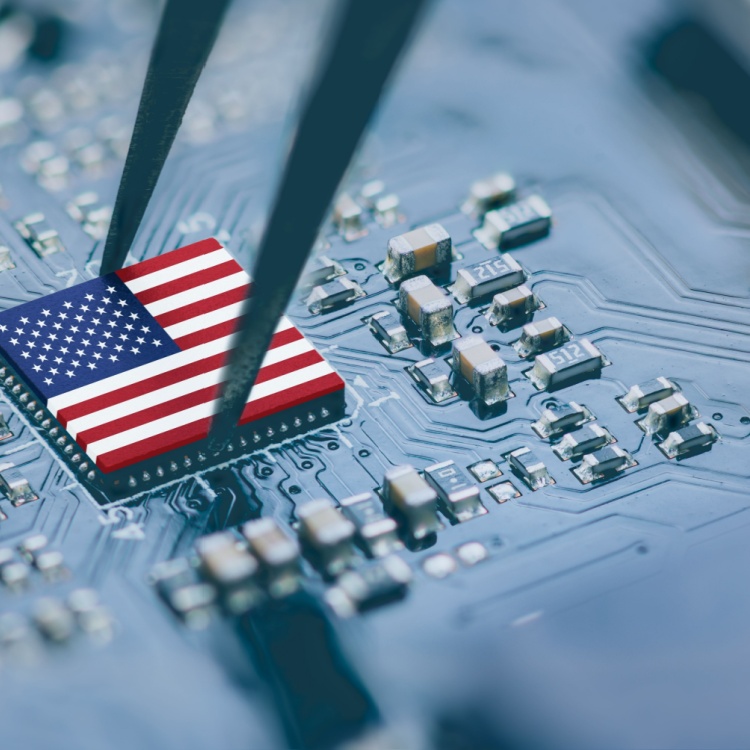
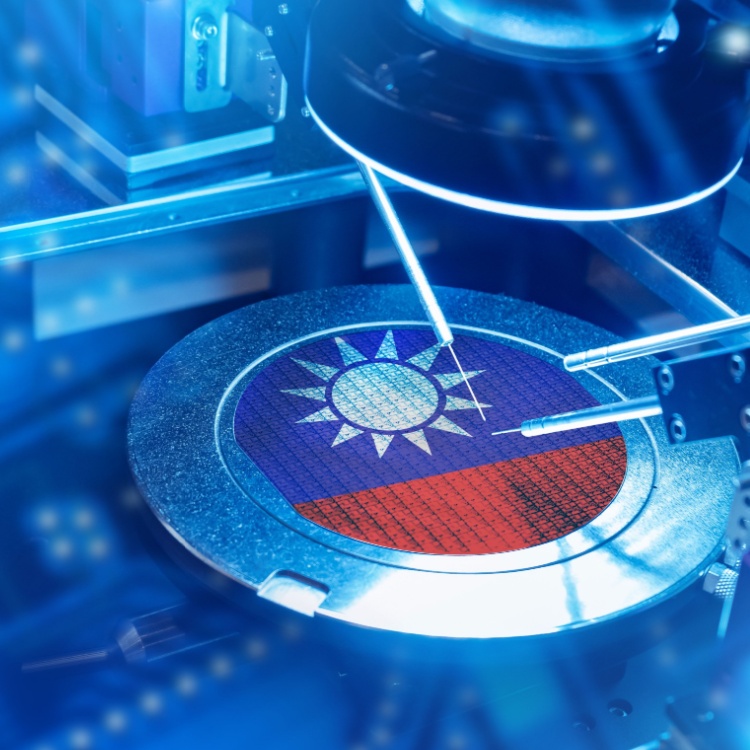
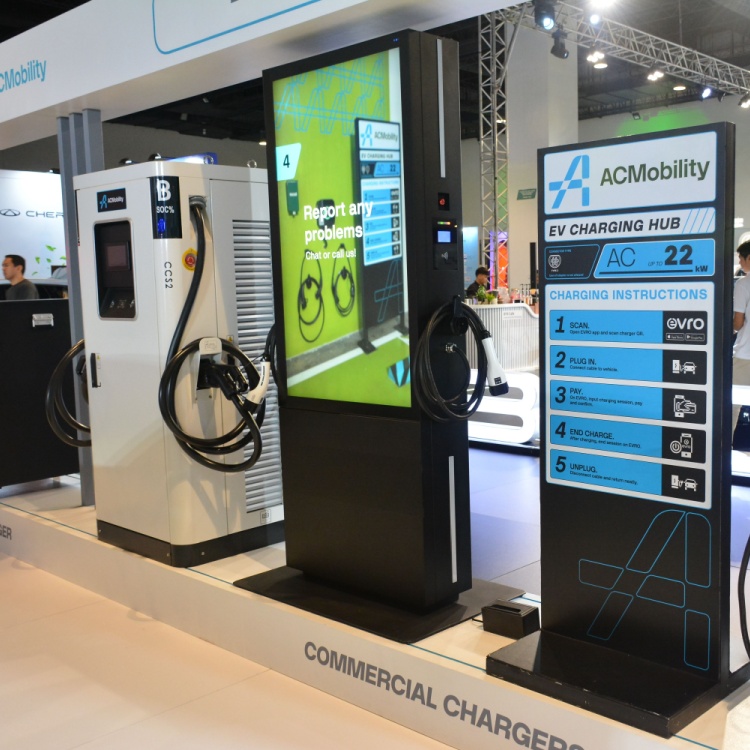