New Product Introduction: What Is It & Why Should You Do It?
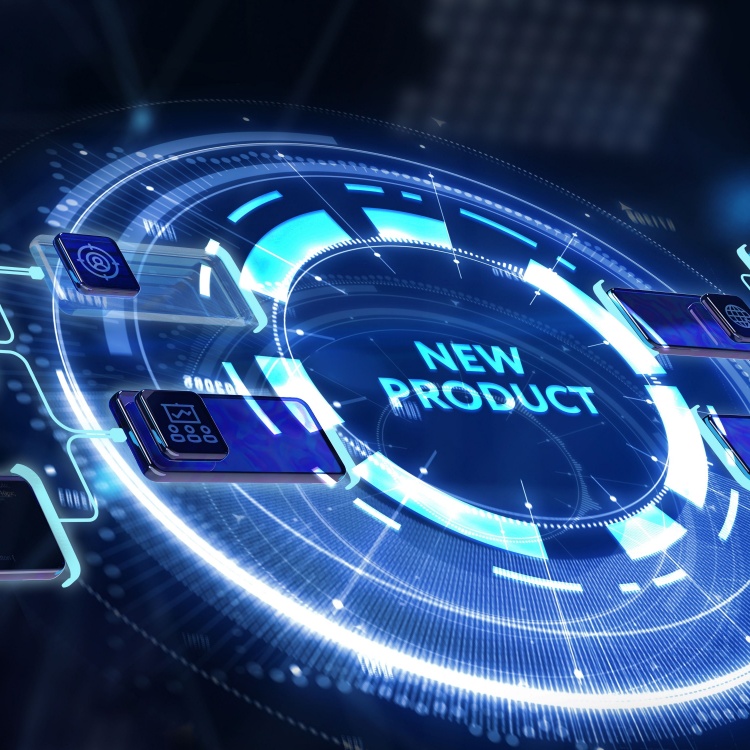
New Product Introduction (NPI) is crucial for global manufacturing companies to stay competitive. It covers the entire process of bringing a product to market, from concept to launch, including market research, product design and development, product testing, manufacturing, and marketing. NPI helps companies innovate, meet customer needs, and stay ahead of competitors.
Before a company launches a product or service, it's hard to grasp the immense effort and work that goes into it behind the scenes before it reaches the public. Although the steps and stages companies follow can vary due to numerous factors, efforts have been made to standardize them into a common framework. This approach helps improve operational efficiency in the New Product Introduction (NPI) process.
NPI transforms an initial prototype into a polished and market-ready product. This involves defining, developing, and launching a new or improved product through several steps. The NPI process is designed from the perspective of the manufacturer.
How do you introduce a new product?
Creating a new product involves managing numerous moving parts simultaneously, requiring careful oversight from the design phase to the initial product launch. The NPI process simplifies this process.
While a dedicated team monitors progress and conducts regular assessments to keep the project on track, allocating adequate resources to each stage ensures a solid foundation for product development. Here are the 8 steps of NPI:
-
Brainstorming and product conceptualization
The NPI process starts with generating product ideas through customer input, industry analysis, and idea generation. During this phase, the team identifies potential product ideas and creates a presentation covering background, objectives, scope, deliverables, budget, stakeholders, and identifying the project manager. Senior leaders review and approve the feasibility. Once approved, the product concept is developed, including attributes, target audience, pricing strategy, and market positioning.
-
Viability assessment and market analysis
Before advancing to product development, a viability assessment is conducted to determine if the product is technically achievable, financially sustainable, and aligns with company goals. Following approval of the product concept, market research begins. This phase involves identifying potential customers and segmenting them based on demographics, preferences, and lifestyle characteristics. Market research is crucial for guiding the product's design.
After completing adequate research, the design and development phase starts, involving close collaboration with design and engineering teams. This step includes maximizing test solutions and refining designs for manufacturing through multiple iterations to assess risks and ensure alignment with market needs. Deliverables include design models, technical drawings, material specifications, and safety reports. Once finalized and approved, the product moves to physical production.
-
Evaluation and verification
In this phase, a Minimum Viable Product (MVP) is developed to verify if the physical product meets design standards. The prototype undergoes rigorous testing to comply with quality requirements and regulatory standards. Market tests provide usability feedback, while pre-production involves inspections and chemical testing of materials and suppliers. If the results are satisfactory, the product progresses to mainstream production.
-
Manufacturing
When the product is market-ready, manufacturing begins. Factories start producing the product according to design specifications. Ongoing monitoring is necessary to ensure adherence to best practices and prevent production issues. Compliance with relevant regulations must be maintained to uphold manufacturing excellence.
-
Product introduction
Supply chain management is essential to avoid delays in component availability and ensure a smooth launch. Accurate forecasting and iterative testing are key to anticipating issues and adjusting designs before full-scale production. Quality assurance throughout prototyping and initial production helps identify and resolve potential problems while running the manufacturing line at full speed can reveal issues before mass production.
-
Mass production
In mass production, optimizing speed and consistency involves effective line arrangement and thorough employee training. Workers should be well-prepared to prevent defects. Assessing and adjusting production lines can enhance efficiency, safety, and reliability. Meanwhile, strong production oversight is essential to prevent delays and ensure success in this critical phase.
-
Post-launch assessment and improvement
After the product launch, continuous feedback and monitoring are essential for ongoing enhancement. Use data from all process stages to identify efficiencies, forecast needs, and adjust manufacturing for cost savings and improved outcomes. Post-launch reviews assess performance, customer feedback, and sales, guiding necessary improvements and optimizing the product's success.
7 benefits of NPI
The benefits of a well-executed NPI process extend beyond initial product success, enhancing overall performance and fostering long-term success.
-
Lowering development costs
By integrating customer needs in the initial stages, you can prevent frequent design changes that increase expenses. This approach not only helps in managing costs but also allows for the introduction of more products and the exploration of new revenue streams.
-
Reduced time to market
By reducing development time, products can be introduced to the market more swiftly. This faster release not only facilitates a faster return on investment but also enables quicker market entry and easier scalability, enhancing overall business agility and growth potential.
-
Boosted product quality
The NPI process ensures that essential tools and practices are in place to consistently produce high-quality products that satisfy customer requirements. This focus on quality enhances product durability and overall performance, leading to greater reliability and a stronger market position.
-
Enhanced manufacturing efficiency
By incorporating best practices in design that align with the manufacturing process, potential issues can be preempted. A robust risk management plan ensures smooth operations while optimizing resource use and improving overall production performance.
-
Gaining a competitive edge
In today’s competitive market, developing the right product at the right time and cost is crucial. A strong NPI process can set your business apart from the competition. Understanding the market, adapting to customer needs, and staying updated with trends boost brand image and growth.
-
Better supply management
Effective NPI ensures that every aspect of the supply chain—sourcing, procurement, distribution, and delivery—is fully prepared to support the new product launch. Furthermore, evaluating how new product introductions affect existing products is crucial for maintaining overall supply chain efficiency.
-
Increased collaboration
Successful NPI programs rely on collaboration across diverse teams—engineering, marketing, sales, and supply chain management—to ensure alignment and smooth execution. Effective new product launches require unified effort from all departments, supported by upper management, and involve extensive cross-functional interaction and coordination.The New Product Introduction (NPI) process is worth adopting because it offers a proven, systematic approach to transforming ideas into successful market-ready products. By leveraging NPI, businesses can enhance efficiency, reduce risks, and drive sustained growth and innovation.
As one of the Top 20 EMS companies in the world, IMI has over 40 years of experience in providing electronics manufacturing and technology solutions.
We are ready to support your business on a global scale.
Our proven technical expertise, worldwide reach, and vast experience in high-growth and emerging markets make us the ideal global manufacturing solutions partner.
Let's work together to build our future today.
Other Blog
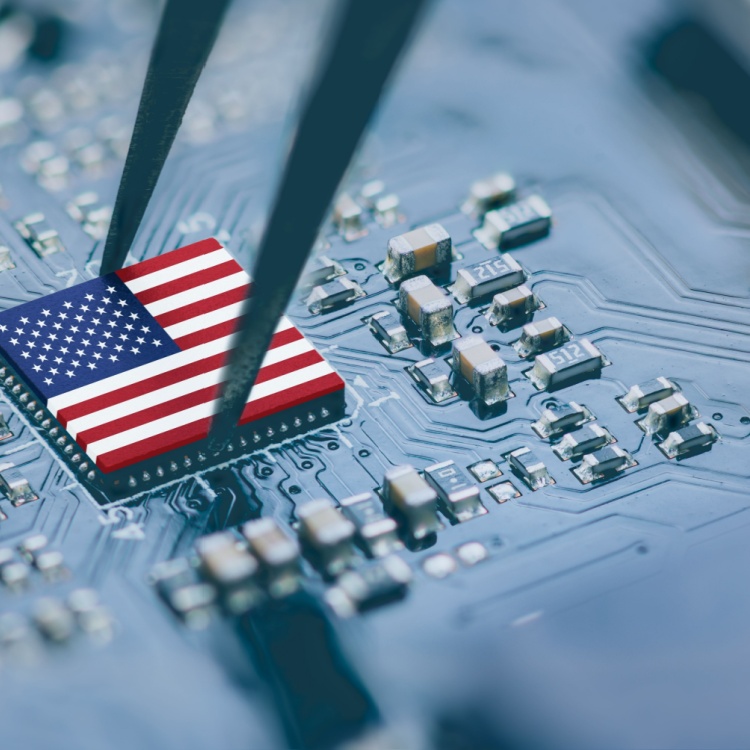
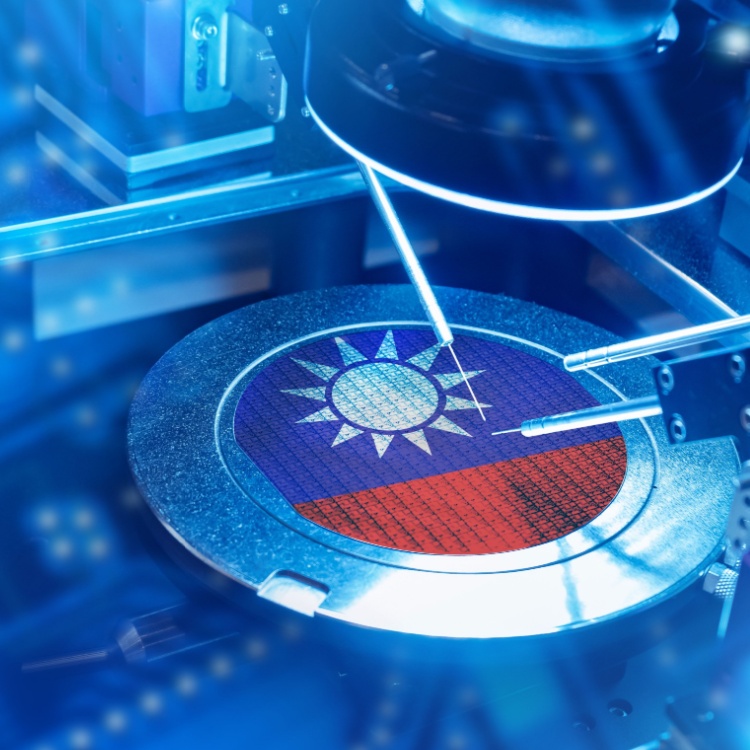
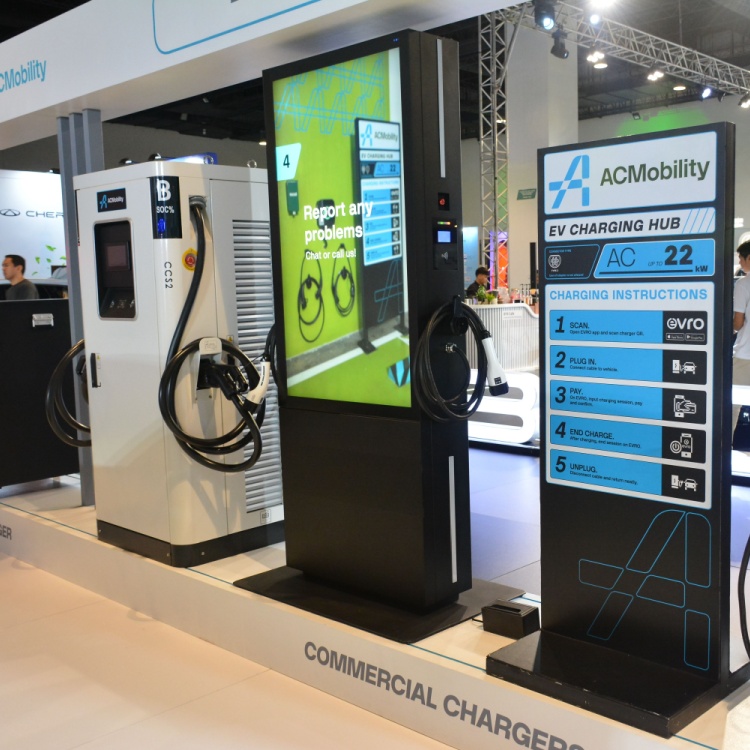