The New Building Blocks of Building
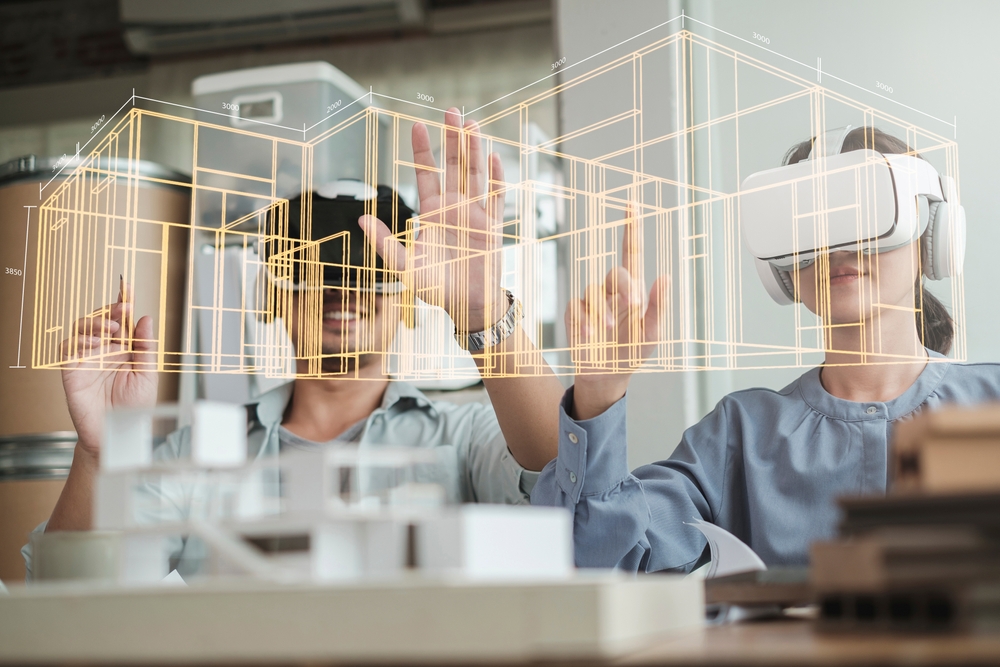
BIM, digital twinning, and construction telematics are some of the innovations that have been introduced in the construction industry. How do these technologies help construction companies build better buildings today?
Industry experts in the arena of architecture, engineering, and construction (AEC) observe that there have been very slow developments in construction productivity in the last thirty years. When compared to the manufacturing industry which has adapted quickly to technological advancements to keep up with global output demands, the construction industry has been rather slow in adopting new technology that already exists.
This perhaps is one factor why profit margins for many construction companies remain low.
According to CBI’s Fine Margin Report, the top 10 largest contractors by revenue’s average profit margin was -0.1% versus an average of 2.6% across the top 100 firms in the United Kingdom.
Experts say that risk allocation and management are two of the largest hurdles that hold back construction companies from increasing sustainable margins, further limiting future investments and promotion of business investments. The more a construction company spends paying for errors that could have been avoided during the planning stages of the project, the more the company’s margins are negatively impacted.
A good example of this is making poorly estimated bids—these run the risk of being too low, or too high. Correcting these poor estimates during an ongoing project can put contractors in a very tight spot.
The Get it Right Initiative (GIRI) says that avoidable errors in construction account for as much as 5% of the project value, and about 21% of the project’s total cost.
While it may be true that adopting the latest in technology can be a very costly investment, contractors need to take into account how holding onto older techniques and tools can cost their companies a lot more in the long run. This is especially true when contractors stand to absorb the risks in every project being undertaken.
In the world of construction, errors, delays, and miscalculations are very costly and wasteful. Most of the budget for each project can be used in better, smarter ways that can boost sustainable margins.
Advancements in BIM and Digital Twinning
In construction, status updates on a project are never static. Data sets are ever-evolving throughout a project’s timeline. For this reason, information needs to be gathered and cascaded to relevant team members.
BIM is the blueprint for every construction project. Digitalization improves the BIM by streamlining data gathering, communication, and storage. Cloud-based technology can help make operations more streamlined and less fragmented. When everyone is on the same page at the same time, it increased productivity and decreases errors.
Digital twinning minimizes errors and risks in execution. It relies heavily on design data inputs such as 2D, 3D, and geographic information systems (GIS). It is also founded on a structure’s pre-construction information such as its health and safety hazards, planning information, and other records. Field notes such as Internet of Things (IoT) data, drone data, inspection, and progress data are also needed for digital twinning.
Construction telematics is an interesting innovation in the field. This allows construction managers to do their jobs more efficiently. Monitoring and reporting on all assets in a single platform, and automating maintenance management for projects are just a couple of tasks made easier.
AI and machine learning can aid construction firms to manage the data collected through many years of projects. The information gathered can help engineers make better-informed decisions on their current projects and avoid making costly mistakes. These technologies can help their firms leverage their knowledge and experience and provide them with an edge over competitors.
On the ground, AI and machine learning improve workers’ productivity and reduce time wasted by unnecessary movements looking for tools around the construction site.
(Also read: *Industrial Wearables) *note: please let me know when the blog post is up so I can insert the hyperlink here
Other technological advancements that support better workflows are machine automation and the utilization of autonomous heavy equipment, which augments physical labor.
What digitalization means for Construction Technology
ConTech has gone beyond 2D, 3D, and 4D modeling. Digitalization in the field of construction covers data analytics, advancements in BIM (building information modeling), site optimization, robotics, operational analytics, and VDC (virtual design and construction).
Ideally, construction companies will have adopted a few of these available technologies to improve business, and experts question why many are still resistant to the idea of keeping up and would rather keep their spreadsheets than level up.
Digitalization means optimizing and empowering construction teams from the back-end office to the engineers on the field. It means making communication clearer and more efficient for everyone involved. The latest, most relevant, and most updated information on each project is cascaded to everyone on a timely basis. Operations run smoother, and risks are minimized.
Best practice workflows are a must when adopting construction technology, for, without a robust workflow, these amazing technological tools become useless.
As one of the Top 19 EMS companies in the world, IMI has over 40 years of experience in providing electronics manufacturing and technology solutions.
We are ready to support your business on a global scale.
Our proven technical expertise, worldwide reach, and vast experience in high-growth and emerging markets make us the ideal global manufacturing solutions partner.
Let's work together to build our future today.