Manufacturing with Collaborative Robots
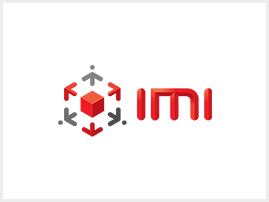
May 17,2019,Philippines—Over the years, the global manufacturing industry has seen several significant and necessary changes in its landscape. Internet integration, automated processes, and even industrial robots—all of these technologies are results of the industry keeping up with the rapid technological advancements and the ever-growing demands of consumers for better and smarter products.
Of course, not everyone feels comfortable with all these changes in global manufacturing. Boston Consulting Group (BCG) in their research The Robotics Revolution: The Next Great Leap in Manufacturing from 2015 shows that the share of tasks performed by robots will rise from the average of 10% to around 25% by 2025, and to some, especially for low-skilled manufacturing workers, this sounds like a threat.
Fortunately, robots will not have to take over every manufacturing job. Human workers can coexist and do manufacturing work with collaborative robots.
What are collaborative robots?
A collaborative robot, or simply cobot, is a robot designed to learn multiple tasks and assist human workers with work that may be too dangerous, strenuous, or monotonous to be accomplished alone. It aims to create a safer and more efficient workplace without necessarily taking away manufacturing jobs from human workers. They are also relatively lightweight and mobile, making them easy to be redeployed from one work assignment to another which is ideal for short production runs.
No programming expertise or software suite are needed to set up and operate cobots. In just a few hours, they can easily be programmed through a tablet or be trained by simply moving its arm in demonstration of the task to be completed.
What cobots can do
From working on circuit boards to loading products into crates—cobots can do anything. As a hand guiding cobot, it can teach a human operator how to hold or move an object the right way. It can also take care of packaging, product testing, and inspection without the need for human supervision.
Like a gift for the ever-challenging manufacturing engineering, cobots are also ideal to be used for electronics assembly and other similar delicate works.
Safety with cobots
Unlike earlier generations of industrial robots, a cobot is designed to have enhanced sensor and vision technology which enables it to work just fine alongside human workers without a need for a cage or to keep distance.
It can sense if something abnormal is in its path, and when it does, it can stop all movement or reverse movement to avoid impact. Some cobots also have a safety monitored stop feature which allows them to work independently until they sense that a human worker will intervene with their operation.
Moreover, cobots are smart enough to identify individual workers through the radio-frequency identification (RFID) tags that workers wear. Cobots are also capable of learning a person’s work habit, and once they have done that, they can be programmed to recognize the same person and then initialize its task.
Effects on the changing workforce dynamics
The global manufacturing industry has always thrived with the advancement of technology, but it came with challenges. One of which is the growing difficulty of manufacturing engineering, and the lack of workers with high knowledge and skills to work with new and complicated technologies.
For this matter, cobots come into the rescue. Easy to program and operate, cobots can guide beginners through their tasks, while they help experienced workers to do more productive and more efficient work.
Robots, especially cobots, are not to be feared of. If its benefits are utilized properly along with the strengths of a human worker, the global manufacturing industry will surely be able to produce better products as well as come up with far more innovative manufacturing solutions for the future.
Other Blog
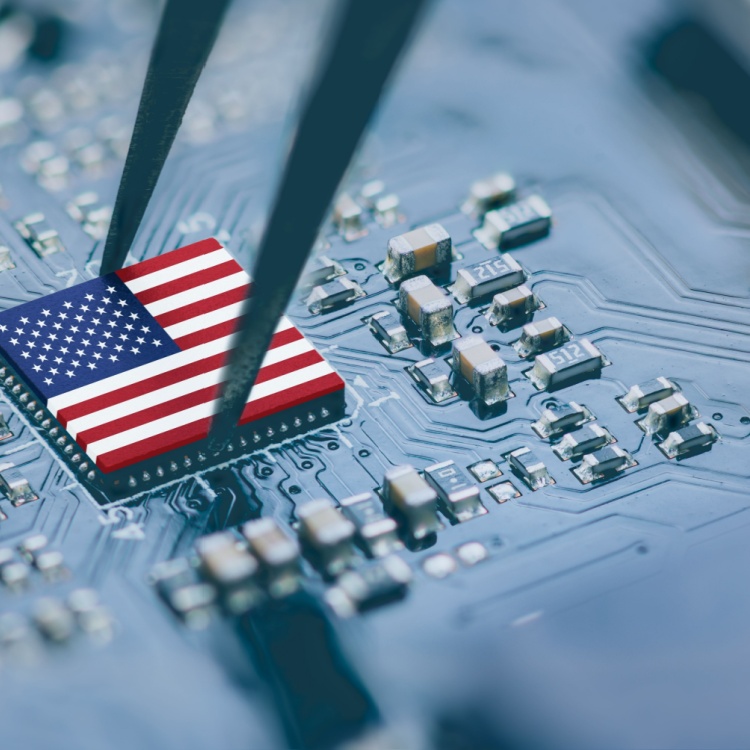
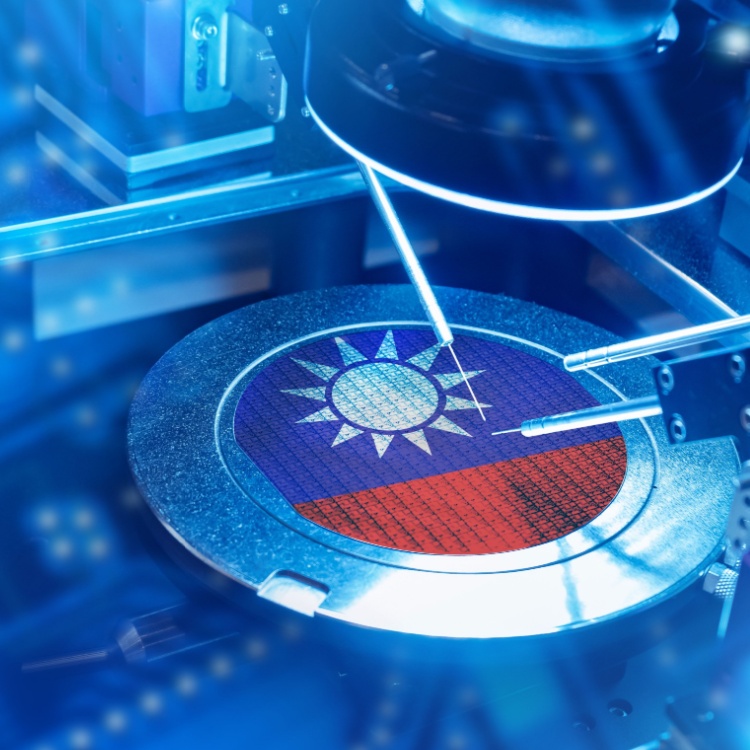
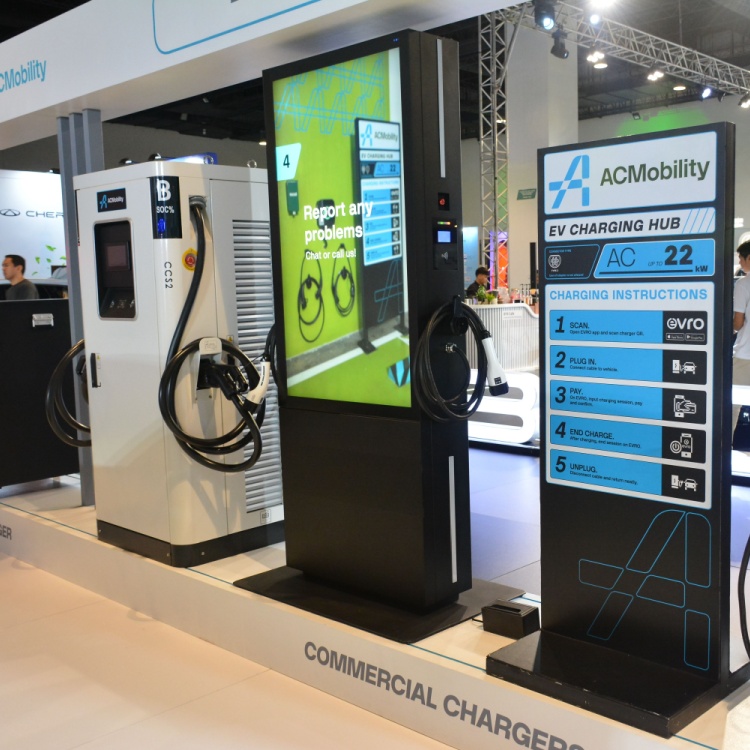