Innovations to Keep Manufacturing Floors Safer
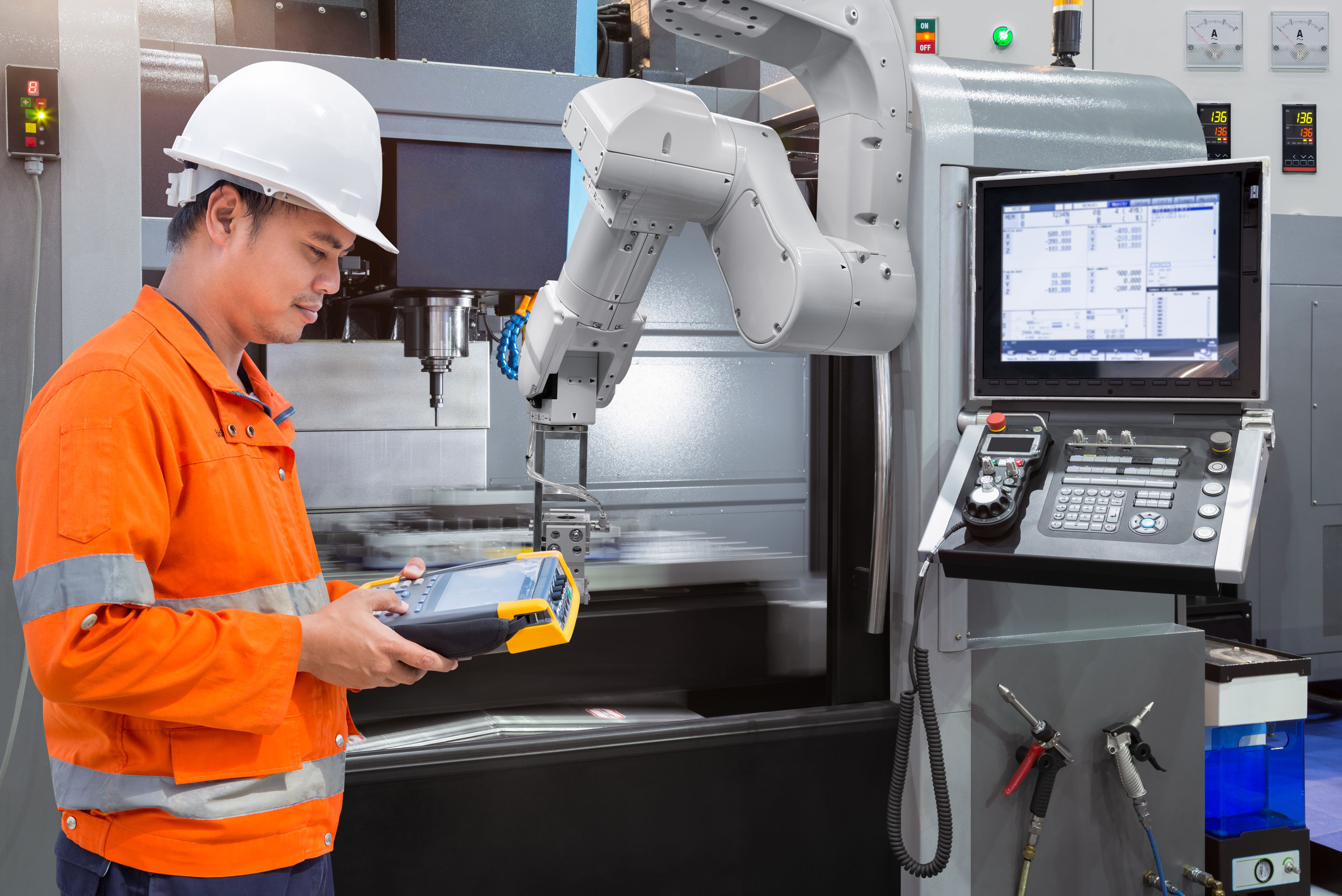
Now that the pandemic has opened our eyes to the risk of infections in the workplace--particularly in manufacturing assembly lines--what new technologies and protocols can we leverage to keep the factory floor safer while maintaining productivity?
The COVID-19 pandemic has disrupted the global manufacturing industry, forcing factories to cut back or halt production for the safety of their employees. As the economy gradually opens, how can companies ensure workplace safety while staying productive and efficient?
In this article, we’ll take a look at the various digital technologies that factories can utilize to mitigate health risks and better monitor employee safety.
Camera feeds and cloud technology to ensure compliance
Camera feeds combined with cloud-based algorithms can analyze images in real-time to ensure that workers are wearing appropriate safety gear and adhering to social distancing guidelines. With thermal imaging, the system can trigger alerts when a worker could potentially have a fever. The algorithms could also analyze trends and patterns on the factory floor, helping decision-makers spot and correct any unsafe processes or security gaps.
Drones, autonomous vehicles, and robots
Autonomous vehicles and drones have the potential to automate functions in manufacturing facilities and warehouses. They can help streamline quality assurance tests and inventory management. They can also automate tasks such as picking goods from warehouse shelves.
Robotics is another technology that can reduce the number of workers who must be physically present on the manufacturing floor. “The lowest-hanging fruit for robotics and AI is to automate the most routine and mechanical tasks that humans do so as to free them up to focus on higher-value tasks,” said Richard Howells, vice president of solution management at SAP Digital Supply Chain.
Robots can remove humans from busy and high-risk environments, reduce their contact with dangerous machinery, and ensure social distancing.
“Artificial Intelligence and robotics don’t take the person out of the process,” Howells continued. “It takes the robot out of the person. People are and will continue to be your most important resource, and giving them the tools they need to do their jobs safely and effectively will be the most important task.”
(Also read: Man and Machine: Collaborative Robots)
Safety apps to activate exposure mitigation plans
Speed is key when preventing an outbreak. When a COVID-19 case is confirmed, safety apps can identify potential exposure and quickly activate an exposure mitigation plan. Containment measures could include turning off access badges, alerting triage teams, activating the deep cleaning of impacted facilities, and tracing affected employees.
(Also read: On the Trail of Disease: Contact Tracing Apps)
Wearable tech
The number of wearable devices around the world has more than doubled in three years and is projected to reach more than one billion by 2022.
Wristbands or smart ID cards could help implement social distance rules, vibrating whenever workers get too close to one another. Smart glasses, smart gloves, and smartwatches, and other PPE can be equipped with sensors to improve workplace health and safety.
Wearable devices connected to the Internet of Things (IoT) could enable real-time monitoring of employee health and location, keeping workers productive, protected, and safe.
(Also read: The Future of Safety: Smart PPE)
Virtual factory acceptance testing
Before installation, factory hardware and technology are typically validated in person by engineers, operators, and suppliers. In this era of social distancing, digital technologies can take acceptance testing off-premises and online.
In a virtual factory acceptance test, testing happens in real-time through multiple high-definition cameras and two-way audio. With multiple cameras, attendees can see various angles of the testing process at one time, and see close-up details of the equipment. These perspectives are not always possible in non-virtual tests.
There are fewer people present on the factory floor, primarily lead engineers who can answer any questions from attendees. A virtual approach to testing means more people can participate remotely and less travel time and costs.
Here’s a video of a virtual factory acceptance test by Schneider Electric.
Remote monitoring
Remote monitoring combines the industrial Internet of Things (IIoT) and artificial intelligence (AI). IoT sensors monitor machine operation and productivity, sending this information to an AI platform for data analysis.
This data can be utilized to monitor equipment performance and utilization, plant operations, inventory, and quality assurance--all while reducing the number of employees present on the factory floor.
With this real-time and historical data, manufacturers can improve production management, equipment maintenance, and employee safety. They can reduce operating costs, prevent costly production stoppages, and maximize uptime.
Here’s a video of IoT manufacturing solutions by Microsoft.
Ensuring productivity while championing safety
While workplace safety has always been the top priority, the COVID-19 pandemic has also created an opportunity for manufacturing leaders to future-proof their business. Accelerating digital transformation could be the key to minimizing risk while maintaining--or even bolstering--production. Organizations that take the steps to champion workplace safety while elevating their digital capabilities will be leading the pack now and in the future.
As one of the Top 20 EMS companies in the world, IMI has over 40 years of experience in providing electronics manufacturing and technology solutions.
At IMI, we believe that humanity drives technology, and we direct our passion at solutions that enhance our way of living. With more than 400,000 square meters of factory space in 22 factories across 10 countries, we are positioned to build your business on a global scale.
Our proven technical expertise, worldwide reach, and vast experience in high-growth and emerging markets make us the ideal global manufacturing solutions partner.
Let's work together to build our future today.
Other Blog
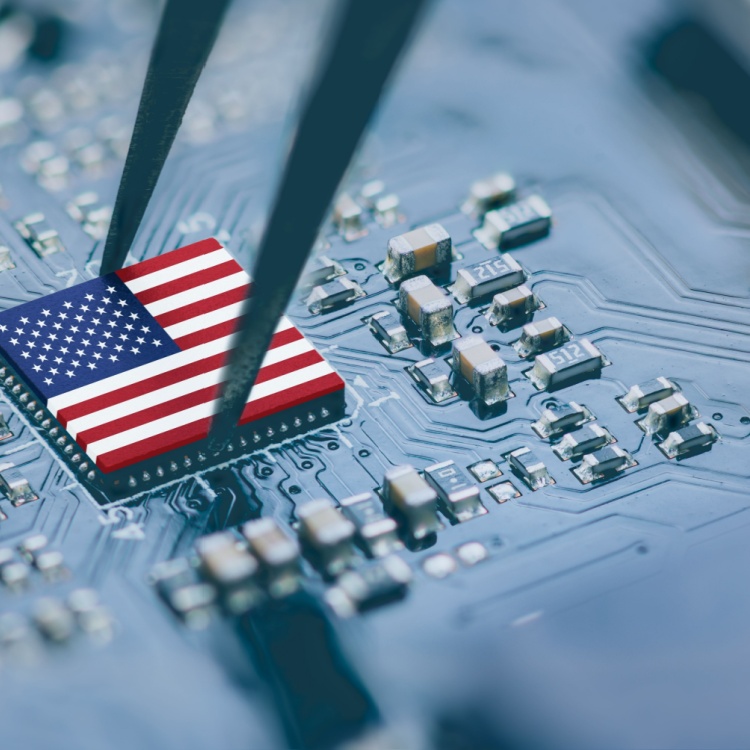
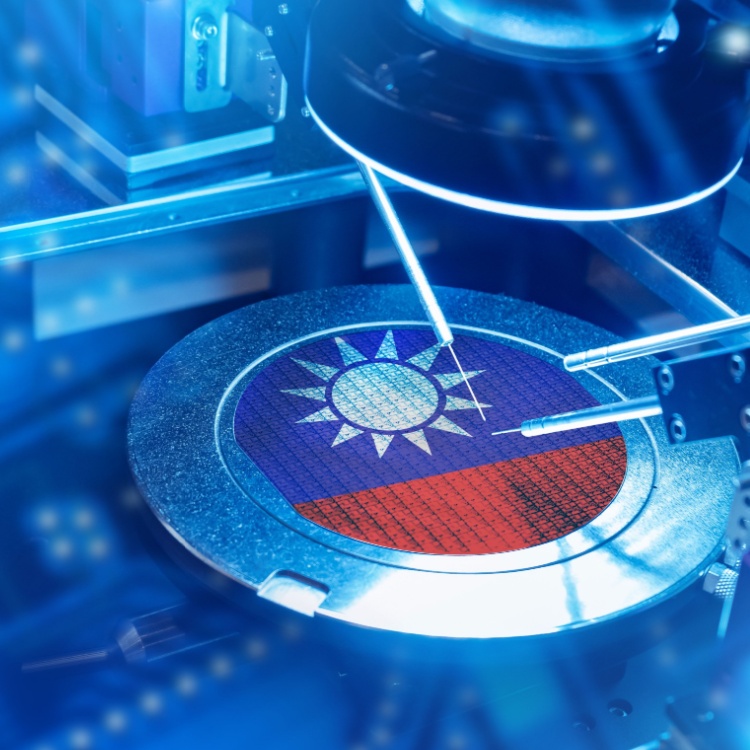
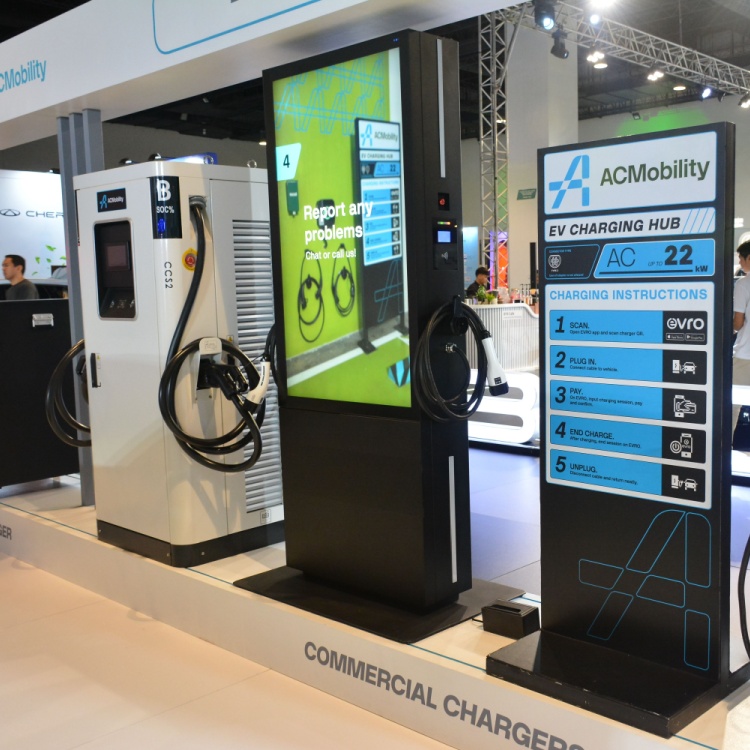