Innovate Your Biz with New Welding Tech
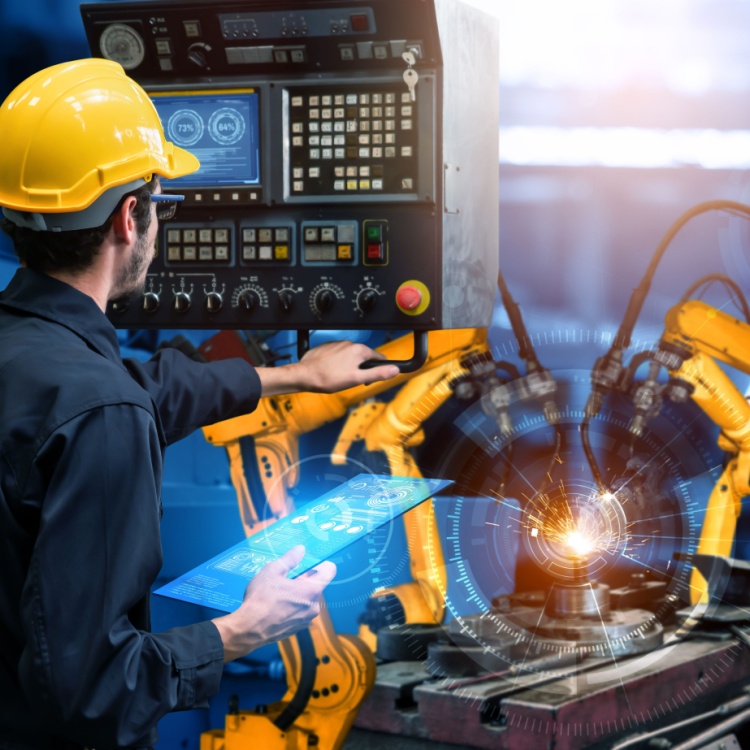
Tool technology, including robotics integration, virtual reality, and lasers, is revolutionizing welding operations and reshaping manufacturing, construction, and infrastructure. The global welding equipment market is forecasted to surpass $15.3 billion by 2026.
Welding, once rooted in traditional artistry, has transformed into a cornerstone of modern industry, advancing alongside societal progress. From forge welding to today’s high-tech methods, innovations in equipment and simulation technologies have improved performance, sustainability, and operational efficiency, making the industry safer and more practical.
7 welding technologies that spark significant change
Advanced welding technologies reshape global manufacturing, driving unprecedented efficiency and precision across industries.
-
Robotics and automation
Robotics and automation have revolutionized the welding industry, sparking advancements in precision machinery and productivity. Robotic welding systems now handle complex tasks with accuracy and minimal human intervention, particularly in sectors like the automotive market and aerospace engineering. These technologies reduce workplace hazards, such as exposure to fumes and strain injuries. Although initially costly, they enhance efficiency, with collaborative robots (cobots) assisting welders in physically demanding tasks.
-
Virtual reality (VR) and augmented reality (AR)
VR and AR welding simulators are advancing welding training by offering innovative manufacturing solutions. VR creates realistic, immersive environments for practicing welding, while AR provides real-time guidance through wearable devices. These technologies deliver immediate feedback, enhancing skill development and reducing errors. By minimizing risks and costs, they offer safer, more efficient training and improve design, planning, and remote inspection, ultimately optimizing manufacturing processes and welding quality.
-
Welding drones
Automation in welding, driven by robots and drones, revolutionizes design and engineering processes. Robotic arms, guided by artificial intelligence (AI), ensure precise, efficient task execution with minimal downtime, crucial for large-scale projects. Welding drones, equipped with sensors and cameras, perform inspections in hazardous or hard-to-reach areas, reducing safety risks. By accessing remote sites, drones cut costs and time, eliminating scaffolding needs and enhancing operations on complex structures.
-
Friction Stir Welding (FSW)
FSW is a groundbreaking technique embraced by engineering manufacturers for its ability to join dissimilar metals without sparks or fumes, offering a cleaner, more sustainable option. By applying friction and pressure, FSW creates strong, precise bonds, making it invaluable in industries like aerospace and shipbuilding. Its defect-free results and ability to handle complex welding tasks have made it a preferred choice for tackling challenging materials.
-
Laser welding
The advancement of laser technology has revolutionized welding in manufacturing markets and industries, enabling the fusion of thicker materials with precision. Innovations like fiber lasers have made this technology more accessible across various sectors. Laser and plasma welding provides high precision, ideal for delicate applications like medical devices and electronics. Laser-beam welding (LBW) ensures consistent, controlled welds, speeding up operations.
-
Gas Metal Arc Welding (GMAW)
This technique uses a consumable wire electrode that melts and enters the weld pool, offering adaptability across various conditions. With advanced power sources enhancing accuracy, GMAW results in smoother and more precise welds. Its fast material deposition, minimal skill requirements, and ability to weld a wide range of metals make it a go-to method in industries for efficient and reliable welding.
-
Tungsten Inert Gas (TIG) Welding
TIG welding, designed for high precision, uses a durable tungsten electrode to create clean, high-quality welds. Modern TIG equipment offers exceptional control, allowing welders to produce finely tuned welds with minimal material waste. This technique is ideal for applications requiring accuracy, such as the production of high-end metalwork. TIG welding is favored for its ability to weld thin materials and produce strong, aesthetically pleasing joints in various metals.
Benefits of welding technologies
Welding technologies have evolved significantly, transforming how industries approach fabrication and joining processes.
-
Boosted productivity
Automated welding systems can complete tasks much quicker than manual welding, greatly boosting production efficiency. In fact, a well-optimized automated system can achieve up to three times the output of a human operator, making it a highly effective solution for increasing welding process productivity.
-
Better weld quality
Weld quality is determined by integrity and consistency. With automation, welding integrity is ensured by electronic controllers that monitor the process. They also enhance consistency by ensuring uniformity in every weld, which minimizes errors and enhances the overall quality of the final product.
-
Improved safety
Advanced welding solutions can operate in hazardous environments, reducing the risk of injury to human workers. Additionally, automation decreases the need for physical labor in the welding process, lowering the chances of injuries and other health issues. This not only boosts safety but also enhances overall efficiency in welding operations.
-
More savings
Welding technologies reduce costs by improving efficiency and minimizing material waste. Automated systems increase production speed and consistency, reducing labor costs. Advanced welding techniques also minimize rework by ensuring higher precision, while reducing energy consumption and material usage. These innovations contribute to cost savings across industries by streamlining the welding process.
Challenges in implementing welding innovations
While welding technologies continue to evolve, there are several considerations to ensure optimal performance and integration.
-
Process complexity
Welding innovations face challenges due to the complexity of the process, involving variables like material properties, joint design, and welding parameters. Achieving precise control over these factors is difficult, and systems must adapt to changes in joint fit-up or material thickness, complicating automation efforts.
-
High upfront costs
The high cost of welding automation equipment may not be justified if the welding volume is low. Additionally, expenses for training staff to operate and maintain the systems must be factored in, making implementation costly for businesses with limited welding needs.
-
Advanced skills
These innovations need skilled operators, but finding qualified personnel can be challenging due to the high demand for welders. Additionally, the expertise required for automation differs from manual welding, making training both time-consuming and costly. This creates difficulties for businesses seeking to implement advanced welding technologies.
-
System integration
Integrating welding automation with current production systems can be difficult. The automation systems must work seamlessly with existing machinery, software, and procedures. Furthermore, adopting welding automation may require adjustments to current workflows, potentially causing disruptions in production and affecting efficiency.
Despite these challenges, welding innovations are crucial for improving consistency, and safety in manufacturing. These advancements enable higher-quality production, reduced costs, and faster turnaround times, helping industries stay competitive while meeting the demands of modern, high-volume markets.As one of the Top 20 EMS companies in the world, IMI has over 40 years of experience in providing electronics manufacturing and technology solutions.
We are ready to support your business on a global scale.
Our proven technical expertise, worldwide reach, and vast experience in high-growth and emerging markets make us the ideal global manufacturing solutions partner.
Let's work together to build our future today.
Other Blog
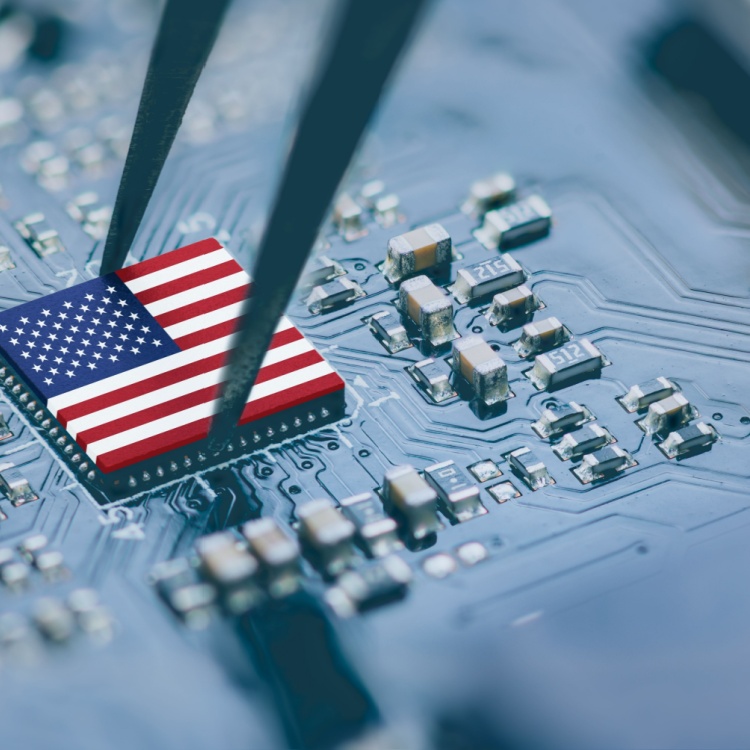
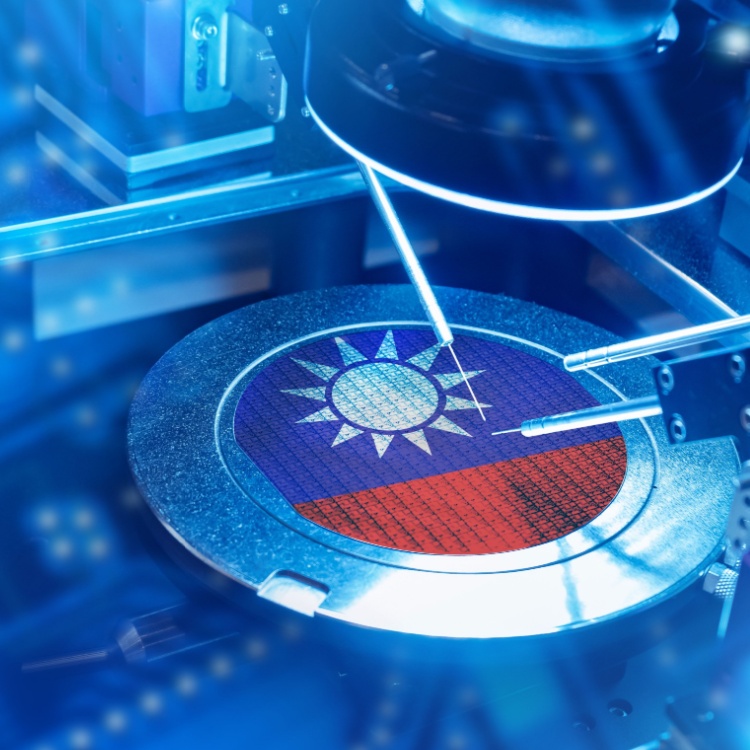
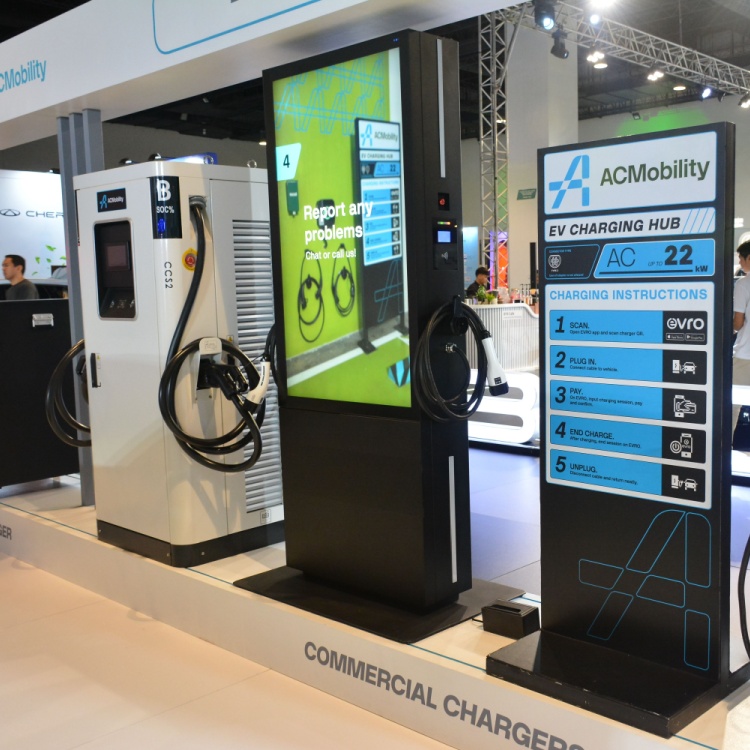