#IMIStories: Breathe
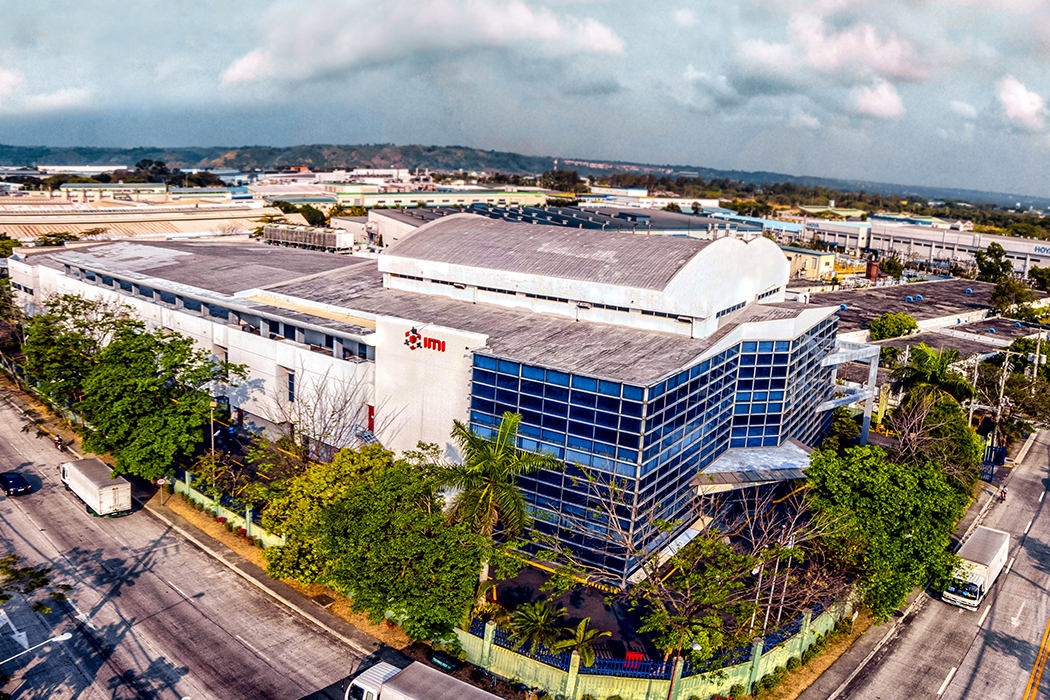
A story of resilience, collaboration, and innovation, Christian Lloyd Silapan, Process Development Engineer (AME) of IMI Philippines, gives us a firsthand account of the local production of a prototype for the UCL Ventura Flow Generator. Designed to ease the breathing difficulties of COVID-19 patients, this affordable continuous airway pressure device (CPAP) is crucial in the country’s battle with the pandemic.
The overwhelming number of COVID-19 patients requiring oxygen therapy shook the global supply chain of ventilators. This is especially true in our country since we have no local manufacturer of these assistive breathing devices.
In April 2020, the Advanced Manufacturing Engineering (AME) group of Integrated Micro-Electronics Inc. Philippines spearheaded the local manufacture of the UCL Ventura Flow Generator. This low-cost, UK-designed non-invasive ventilation system was specifically developed for COVID-19 patients with breathing difficulties.
The assistive breathing device is yet to be officially released to the Philippine market. The story behind its localization was not a straightforward route, but we persevered, committed to delivering this life-saving technology to our countrymen.
During the first phase of the project, everyone was enthusiastic, though a bit hesitant. After months in Enhanced Community Quarantine (ECQ), team members had to leave their homes. Our goal was to build five working prototypes. These were to be used as initial test units for the company’s partner hospitals. They were also needed for registration with the Food and Drug Administration of the Philippines (FDA).
Little did we know that the initial build was going to be a struggle: What we originally planned as a one-week prototyping schedule stretched to more than three weeks due to unforeseen events.
“Since all the preparations were hectic, I had to leave my one-year-old at home to stay at the plant.” – Rozana Sison, Process Development Technician (AME)
In the beginning, we had difficulty working with our suppliers. Their limited manpower due to lockdown affected the supply of the raw materials needed for our prototypes. On top of that, most of the device components failed to meet the required specifications. Despite these issues, the team did not stop exhausting all options to overcome these hurdles. With the team’s resilience and assistance from our in-house fabrication facility, we successfully manufactured the working prototypes. It was a significant win for the team and the country.
“We had to make sure that the prototypes were working. I even used the device myself to ensure that it’s functioning well.” – Ed De Guzman, Process Development Engineer (AME)
Everyone thought we were on a roll. We had acquired FDA approval for IMI Philippine’s License to Operate (LTO) and had received the Certificate of Medical Device Registration. And then, one of the greatest fears for 2020 came true: three members of our team tested positive for COVID-19.
As part of the company’s protocol, the team underwent diagnostic testing and was required to complete home quarantine. Fortunately, no one else contracted the virus. But, the manufacture of the Flow Generator Kit was greatly affected as the work was done in our manufacturing plant. When you are in the manufacturing industry, there is only so much you can do when working from home.
Collaboration was key to making the remote setup work. The manufacturing team, including Quality, Engineering, Materials, Warehouse, Test and Systems Development, and Sales Group, threw their support behind AME to push the project forward.
“This was a challenge for us because aside from the limited resources we have, time was of the essence. We needed to adapt well and move fast.” – Archie Miranda, Principal Engineer (AME)
After months of patience, problem solving, and teamwork, AME and the rest of the team at IMI Philippines are now ready to mass-produce the device for use in the country.
For the first time in its forty-year history, IMI will be manufacturing a product with the company name engraved on it. I take it as a sign to never back down in helping COVID-19 patients breathe. It motivates me to do all we can to protect the safety of our healthcare workers. Etched on each device is IMI’s dedication to harnessing technology to improve and save lives. In this global fight, every breath counts.
As a Process Development Engineer for the Advanced Manufacturing Engineering (AME) Group, Christian is responsible for providing technical value-added services for manufacturing capability build-up and process development for new contracts. Together with the rest of the AME Group, he focuses on new and advanced processes and material technologies to drive new business opportunities for IMI. Christian graduated with a Bachelor of Science degree in Materials Engineering from the University of the Philippines and has been with IMI since September 2019.
Some of the key team members behind the UCL Ventura Flow Generator. From Top Row (L-R): Jiwee, Carol, Penny, Ed, Arnel, Gliz, Carla, Len, Jay, Nick, Noel, Winston, Edil, Aklen, Jeff, Lloyd, Fats, Luke, Nan, Archie, Mike, Almond
As one of the Top 20 EMS companies in the world, IMI has over 40 years of experience in providing electronics manufacturing and technology solutions.
At IMI, we believe that humanity drives technology, and we direct our passion at solutions that enhance our way of living. With more than 400,000 square meters of factory space in 22 factories across 10 countries, we are positioned to build your business on a global scale.
Our proven technical expertise, worldwide reach, and vast experience in high-growth and emerging markets make us the ideal global manufacturing solutions partner.
Let's work together to build our future today.
Other Blog
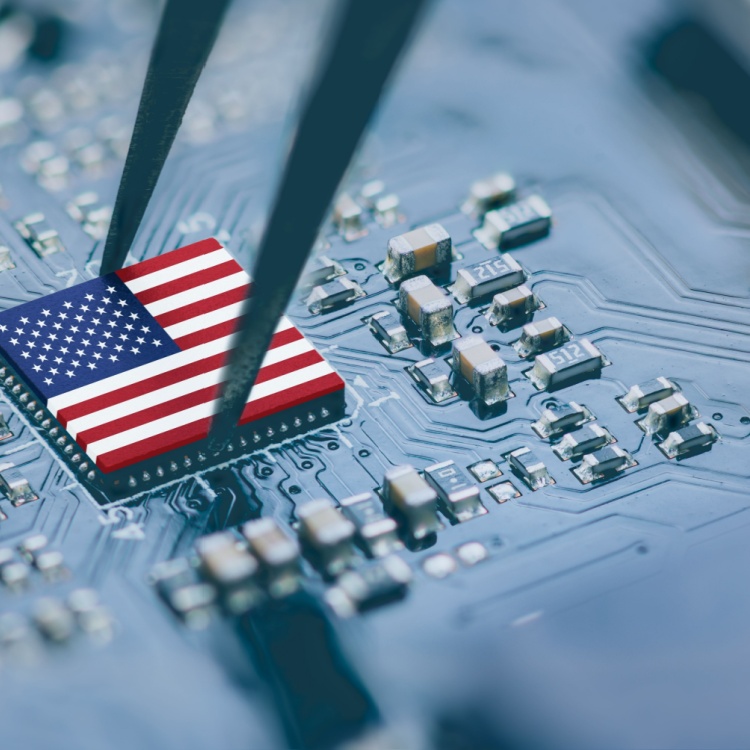
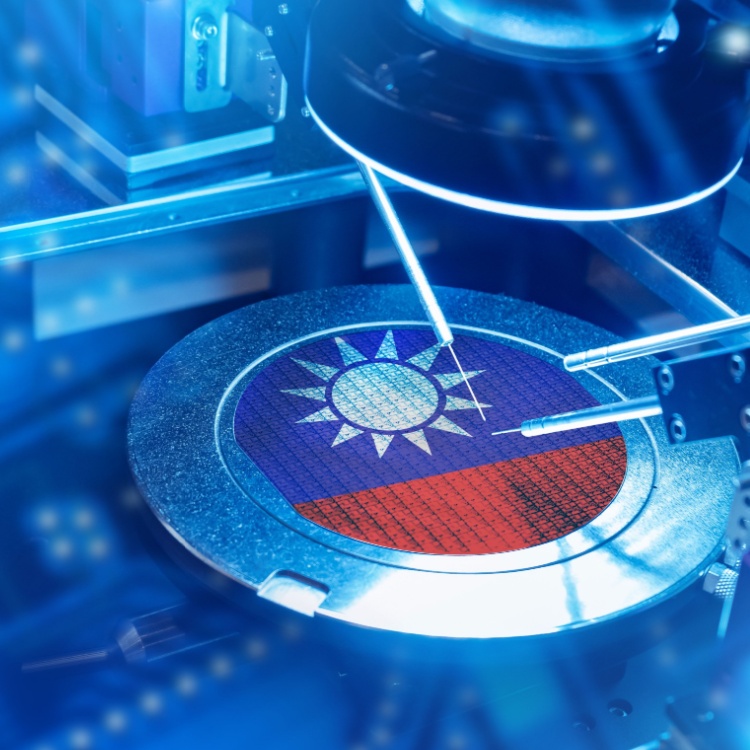
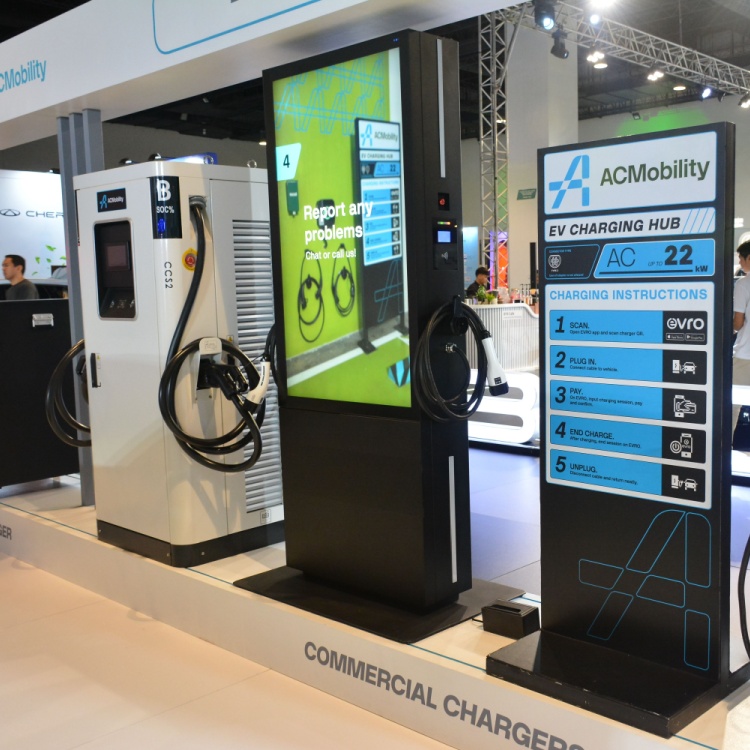