How to Revamp Just-In-Time for Present Times
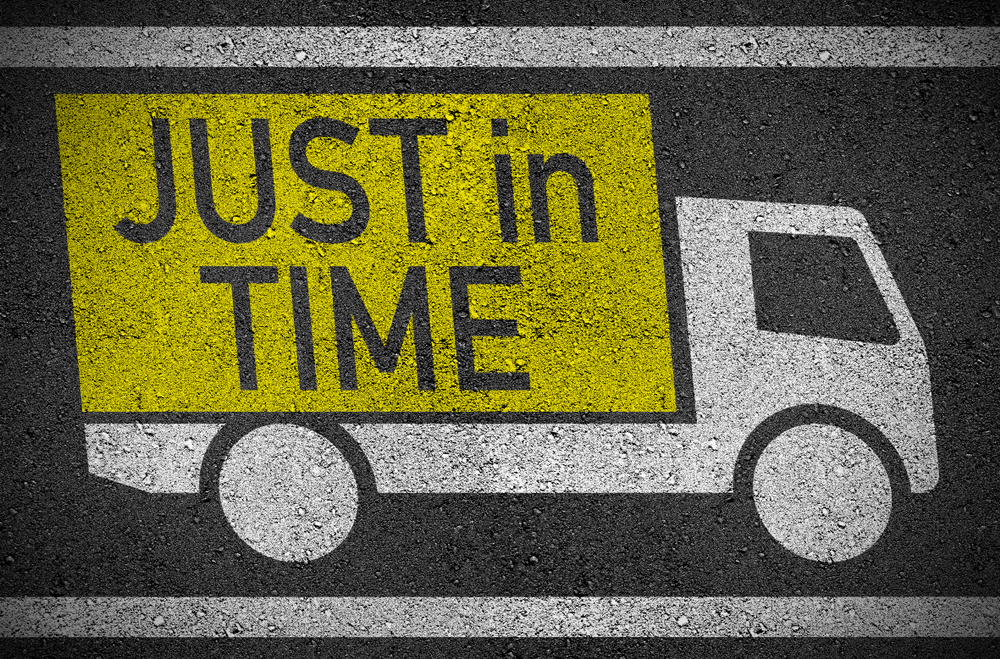
As a response to the many major disruptions in the supply chain, Just-in-time (JIT) models have given way to just-in-case. Industry experts say: don’t write off JIT just yet.
Just-in-time (JIT) is a method of managing inventory that can be traced back to the early days of Toyota. It involves receiving goods only as needed. Today, most companies have adopted JIT as a framework for supply chains and is considered one of the pillars of large industries.
However, in recent times major disruptions such as the global pandemic have irrevocably changed so much about the way we do things, that many companies have adopted other models, such as “just-in-case”, to keep their companies afloat. Instead of only ordering supplies on an “as needed” basis, companies have been overproducing to cover gaps caused by major disruptions.
(Also read: Experts Weigh In On Supply Chain Trends)
The just-in-case model was a natural and organic response to the unpredictability and uncertainty brought about by the pandemic. When presented with limitations such as widespread lockdowns, it seemed only natural to respond “just in case” things do not get better. However, this model does not seem very practical in the long run.
The Just-in-case model presents its share of problems, too. A surplus or excess of inventory is one of them, and this trickles down to problems such as waste for the company, and a downturn in profits. Moreover, experts say that just-in-time does not necessarily help in strengthening the resilience of a company, but rather, could hurt it in the long run.
So what are companies to do?
Pivoting Just-in-time
Has JIT become obsolete in today’s economic climate? Industry experts are split on this topic. Many may argue that after the pandemic, our world has changed, and therefore so must the old ways of doing things. Yet, while this holds some truth, there is also wisdom in pivoting yet again and reviewing how we can tweak the old and make it new.
SupplyChainDive asked a few key industry leaders their thoughts on JIT’s relevance in today’s world. Interviewing CEOs of consulting companies as well as management academics, the key takeaways involved synthesis and a more nuanced approach to changing times. While these experts agree that “the old” JIT has more limitations now compared to pre-pandemic times, to do away with JIT completely would be a mistake.
Lisa Anderson, CEO of LMA Consulting says that while JIT is not dead, “the days of taking the concept literally and ordering inventory ‘just-in-time’ is…Executives have realized that the supply chain is a system of systems, and no one can control the end-to-end supply chain.”
The Harvard Business Review says not to abandon JIT just yet. Rather than eschewing JIT completely, authors ManMohan S. Sodhi and Thomas Y. Choi presented their case for revamping JIT, not rejecting it.
The authors echoed key sentiments from the SupplyChainDrive interviews: it would be unwise for businesses to abandon JIT altogether as it would hurt the company’s performance. The authors stood by JIT’s efficiency as a system of production, especially with today’s growing interest rates. However, revamping JIT is a must.
It entails creating stockpiles and/or manufacturing buffers to protect operations from disruptions. Offering two case studies for each, Toyota and Volkswagen, respectively, the authors gave a clear bird’s eye view of how these strategies were successfully implemented.
As Lisa Anderson said in her interview, the supply chain is a system of systems, and the way to revamp JIT is by redesigning the JIT network. Companies need to think of it as making many more chains in the link of supply chains, and the way to leave nothing to chance is to step in and do the analytical work. This means mapping the supply chain extensively.
The next step the authors delved into was for companies to identify which segments of the supply chain can be run on a JIT basis. Toyota was able to identify which segments were most vulnerable to disruptions and then built a business continuity plan for stockpiling based on timelines. On the other hand, Volkswagen built buffers for its JIT plants by putting up battery factories to ensure a continuous supply.
The authors also recommended assessing the supplier relationship, which leads back to the first recommendation: mapping the supply chain extensively. Not all supplier relationships are close, some are transactional, and it would benefit companies to know when to collaborate and when to keep things transactional.
Many of their ideas look great on paper, so it’s up to companies how to execute and implement these into their operations. Reading between the lines, an ordinary consumer gets the impression that what is needed is a careful assessment of what these companies already have, as well as some old-fashioned teamwork (even between and among competitors).
JIT has not died, not by a longshot, but it needs to transform with the changing
times.
As one of the Top 19 EMS companies in the world, IMI has over 40 years of experience in providing electronics manufacturing and technology solutions.
We are ready to support your business on a global scale.
Our proven technical expertise, worldwide reach, and vast experience in high-growth and emerging markets make us the ideal global manufacturing solutions partner.
Let's work together to build our future today.
Other Blog
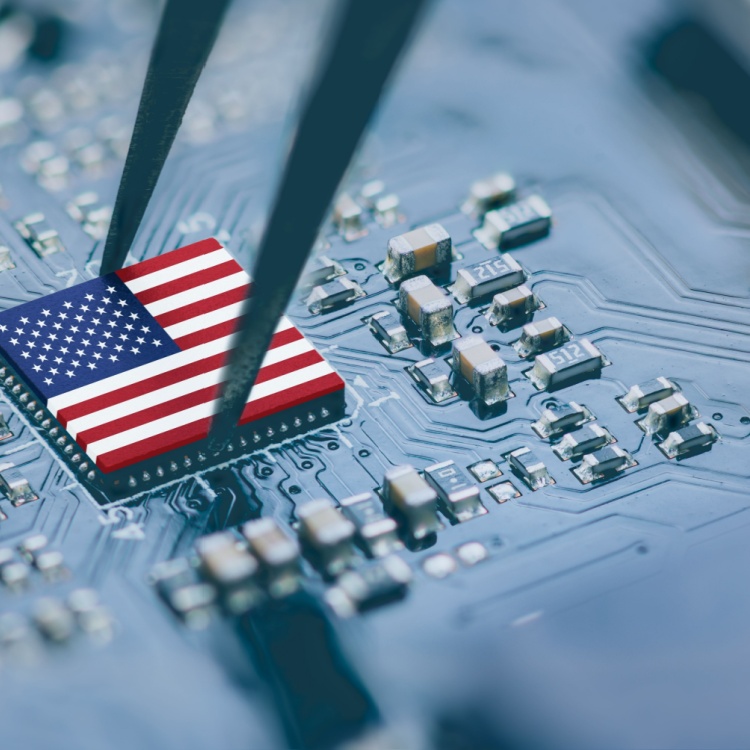
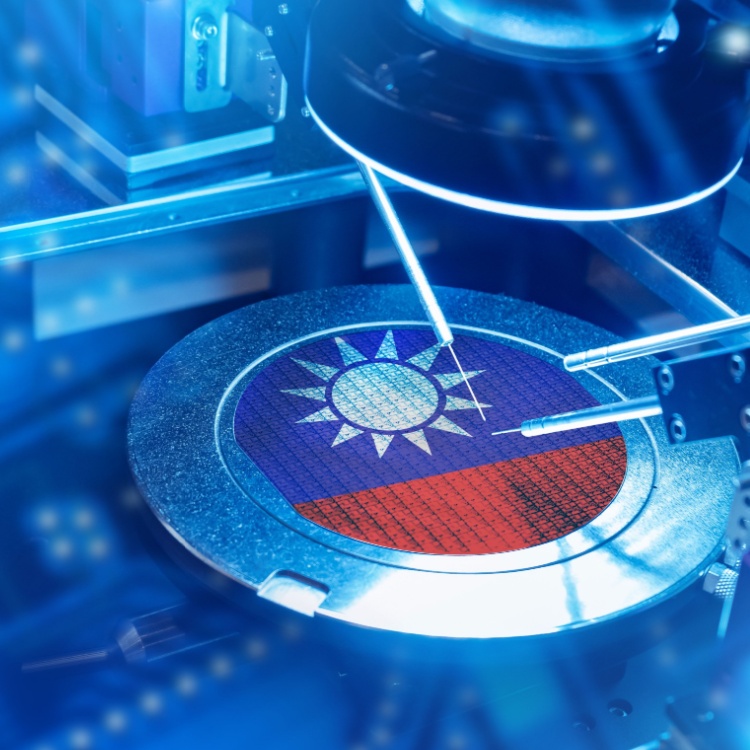
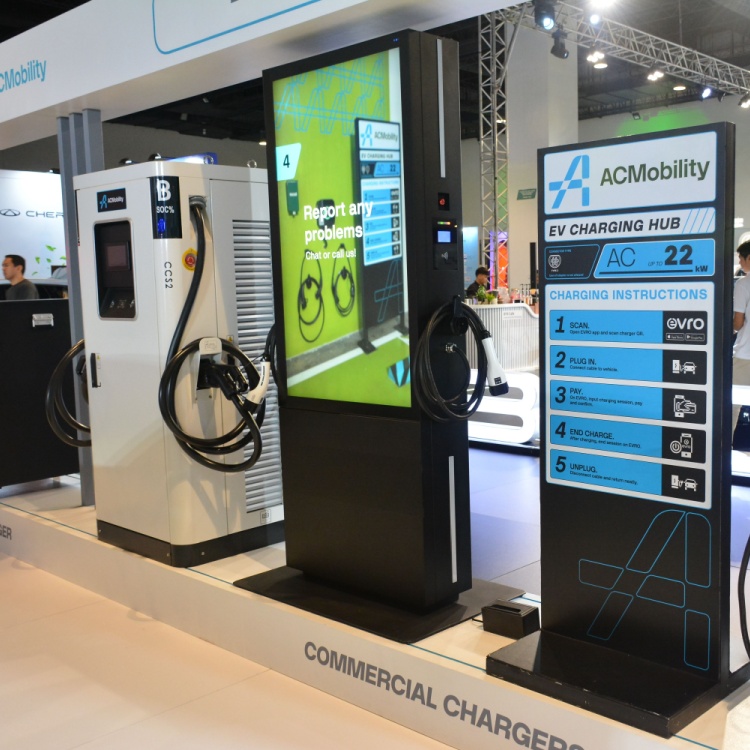