Hitting It Big with Small Things
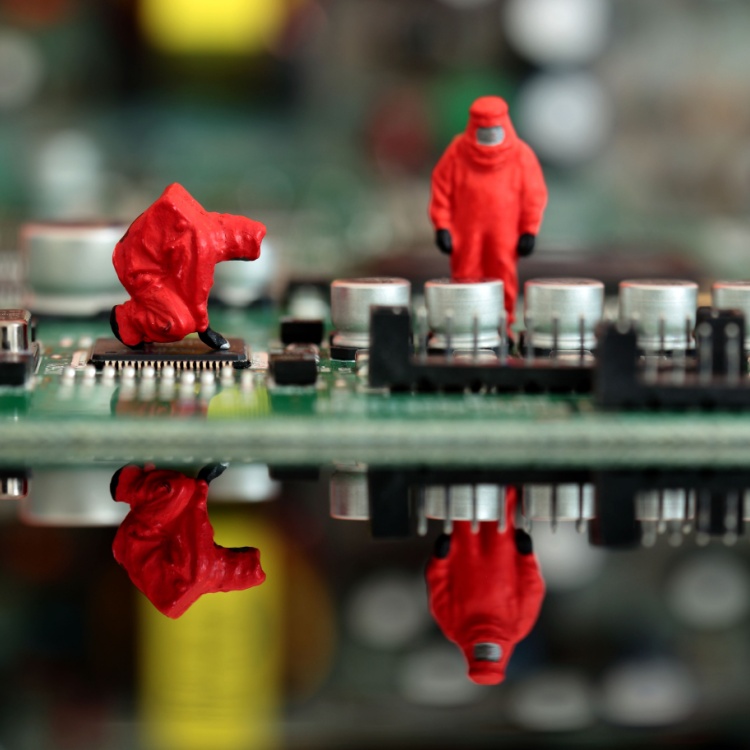
The drive for smaller, portable electronic devices has fueled industrial markets for decades. Miniaturization is essential for manufacturers to stay competitive, as compact products integrate seamlessly into daily life, are easier to carry, consume fewer materials, and often last longer due to reduced power usage.
Miniaturization is the process of shrinking parts, gadgets, or frameworks while retaining or enhancing their capabilities and effectiveness. In electronic manufacturing services (EMS), miniaturization plays a pivotal role, allowing for the development of compact, lightweight, and more powerful tools. This approach has been instrumental in advancing industrial manufacturing solutions, fueling the creation of cutting-edge, high-performance electronics in smaller forms.Fields that benefit from miniaturization include:
-
Life sciences
Miniaturization benefits life sciences by enabling the development of compact, portable medical devices, advanced diagnostic tools, and wearable health monitors. These innovations allow for real-time data collection, improved patient care, and enhanced research capabilities, ultimately advancing healthcare accessibility and personalized treatment options.
-
Electronics
In electronics, miniaturization has driven the creation of smaller yet highly capable computers, mobile phones, and similar gadgets. For instance, reducing the size of transistors has enabled the design and development of improved products like microprocessors containing billions of them. This allows for rapid, real-time data processing and supporting advanced applications that require substantial computing power in compact forms.
-
Aerospace engineering
Miniaturization has enabled lighter, more efficient components like micro-sensors, gyroscopes, and transceivers essential for aerospace applications. This advancement supports the creation of smaller, agile spacecraft and allows for launching increased payloads into orbit, enhancing mission capacity and flexibility in space exploration.
Benefits of miniaturization
Miniaturization often comprises the latest news in the manufacturing industry because of its transformative benefits.
-
Handiness
Portability allows devices to be lightweight and easy to transport. This enhances user convenience, enabling seamless integration into daily life and facilitating access to technology anytime and anywhere.
-
Tech innovation
Miniaturization helps make tech advancement possible, leading to innovative design for manufacturing processes. This allows for the creation of sophisticated, compact devices that improve efficiency and functionality in various industries.
-
Improved performance
When there’s less distance between components, quicker processing and lower latency are possible. Increased density leads to shorter signal paths, enabling smaller electronics to achieve greater speeds and clock rates.
-
Sustainability
Miniaturized components typically require less power, resulting in energy-saving technology. This reduced energy consumption enhances performance and supports sustainable industrial solutions, making innovations more environmentally friendly and cost-effective over time.
-
Lower costs
Compact devices typically utilize fewer materials, resulting in significant cost savings. This reduction not only lowers production expenses but also facilitates system integration, making it easier to create streamlined manufacturing methods.
-
Wearable electronics
Miniaturized components play a crucial role in creating lightweight and comfortable wearable gadgets. Their integration not only enhances user experience but also adds significant economic value by driving innovation and expanding market opportunities.
-
Space efficiency
Miniaturized devices are perfectly suited for industries facing space limitations, including aerospace and automotive markets. Their compact design enables efficient integration into tight environments, enhancing functionality while meeting the specific demands of these industries.
Challenges of miniaturization
Shrinking technology presents a unique set of challenges to maintain performance at reduced scales.
-
Heat management
Miniaturized components are often densely packed, increasing the risk of heat build-up. Effective thermal analysis is essential, as inadequate heat dissipation can affect performance and durability, potentially causing electronic devices to fail over time due to excessive internal temperatures.
-
Production intricacy
Miniaturization increases manufacturing complexity, requiring advanced assembly methods and precision machinery. As components shrink and ultra-fine pitches become common, challenges in placement, rework, and bridging risks arise. Customized processes and expertise are essential for accurate, high-speed assembly.
-
Product design specifications
Designing for manufacturability is essential in advancing miniaturization. Selecting and combining the right production techniques during design ensures functionality and addresses technical challenges. Robust manufacturing capabilities are crucial for producing custom components at scale, balancing cost, quality, and reliability for high-performance applications.
-
Signal strength
Placing components closer together increases the risk of electromagnetic interference (EMI) and signal overlap, complicating signal integrity and potentially impacting device performance. In critical electronic devices, continuous reliability is essential. Designers can mitigate EMI by incorporating metal shields or conductive barriers around sensitive components.
-
Risk of physical damage
Smaller components often face increased vulnerability to physical damage from shock or oscillation. Ensuring the resilience and sustained dependability of miniaturized devices poses a considerable challenge, necessitating careful Material Composition Analysis to select appropriate materials that withstand these demanding conditions.
Things to consider when miniaturizing
Before pursuing product miniaturization, it is vital to acknowledge several important factors, as the process involves complexities beyond the seemingly simple act of reducing size.
-
Material quality & functionality
Not all materials perform equally, particularly at the nanoscale. It is essential to select materials capable of being manufactured into tiny components without compromising durability or performance, which may necessitate innovative production techniques and joining technologies. Using high-quality materials enhances overall outcomes and enables unique combinations of characteristics.
-
Production strategies
Miniaturized components are created through techniques such as microfabrication and nanofabrication, employing specialized tools for tiny assemblies, such as microchips. Advanced robotics and high-precision manufacturing processes are crucial for achieving accuracy at a microscopic level, enabling rapid market adaptation while minimizing errors and enhancing product quality.
-
Design choices
Innovative design drives the trend toward smaller products, enabling reduced component count and integrated functionality. Techniques like Design For Assembly (DFA) and Design For Manufacturing (DFM) support the design and engineering workflows. By creatively combining multiple functions into fewer materials, it is possible to achieve more compact product designs.
-
Power consumption
Smaller products typically require more compact batteries, yet the goal remains to achieve long-lasting performance. This creates a delicate balance where efficiency becomes paramount, as it is essential to minimize power consumption without sacrificing functionality. By innovating battery technology and optimizing design, manufacturers can enhance energy retention while ensuring the product remains compact and effective.
In conclusion, miniaturization is vital to technological advancement, driving innovation across industries. It enables the creation of smaller, more efficient devices, enhancing performance while reducing energy consumption. As more sectors embrace miniaturization, the potential for transformative applications and improvements in quality of life will expand, significantly reshaping the future of technology.As one of the Top 20 EMS companies in the world, IMI has over 40 years of experience in providing electronics manufacturing and technology solutions.
We are ready to support your business on a global scale.
Our proven technical expertise, worldwide reach, and vast experience in high-growth and emerging markets make us the ideal global manufacturing solutions partner.
Let's work together to build our future today.
Other Blog
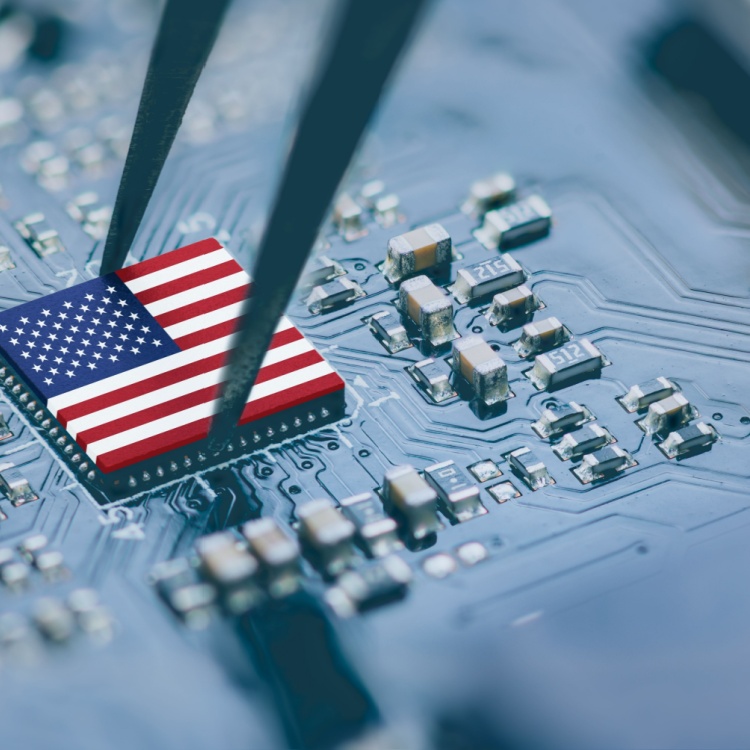
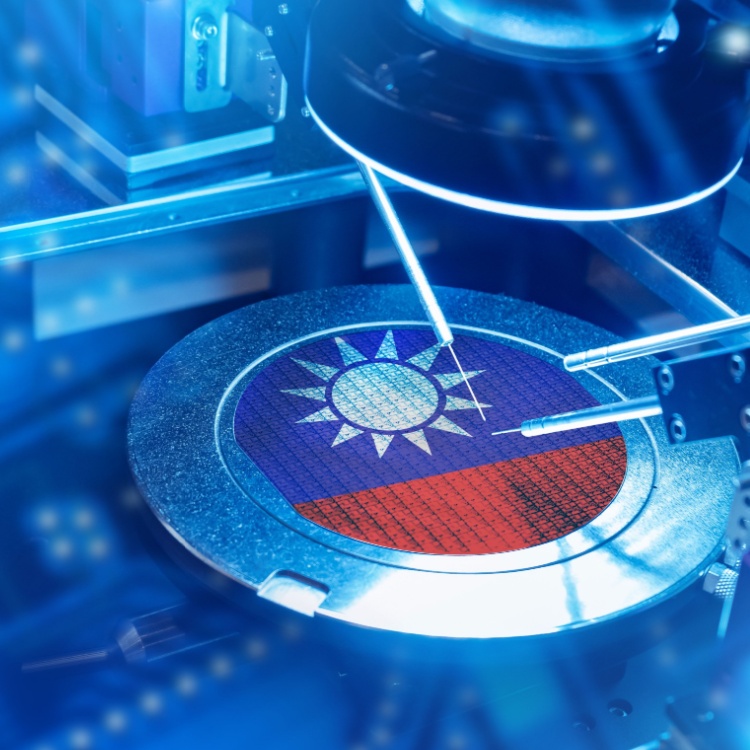
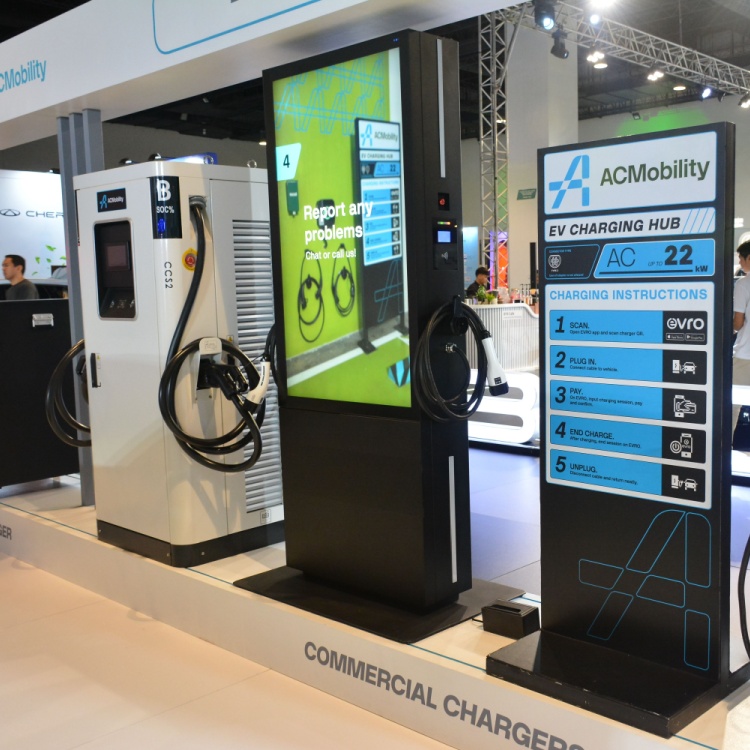