Gen Z: Why Manufacturing Is a Great Career for You
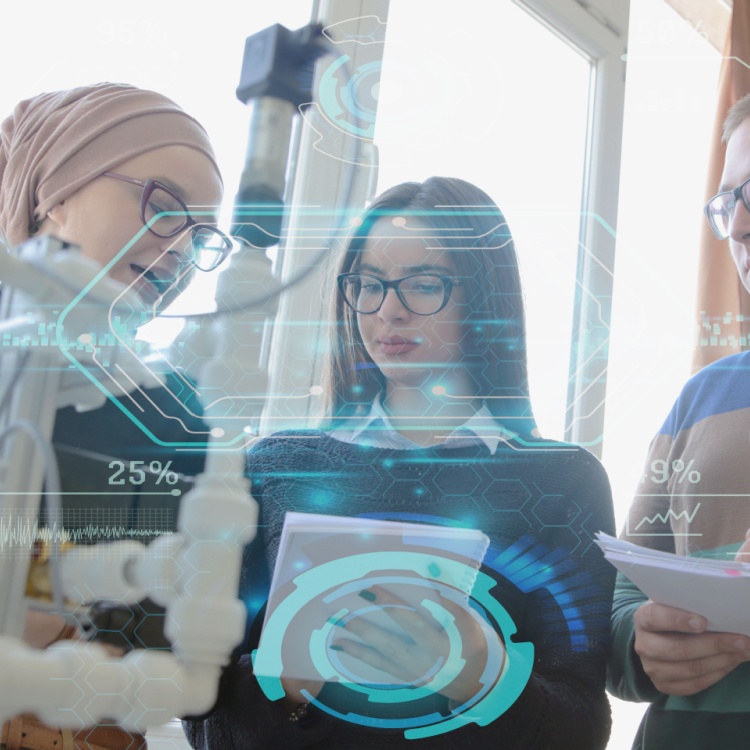
Gen Z is open to manufacturing jobs, but to attract and retain them, the industry must shift from a machine-focused environment to one that prioritizes people. This is especially important because by 2030, Gen Z will comprise 30% of the U.S. workforce, yet nearly half of those currently in manufacturing markets and industries plan to leave within six months.
The global manufacturing sector is evolving, facing both workforce challenges and transformative opportunities. Digital advancements like artificial intelligence (AI), robotics, and IoT are pivotal in addressing the skills gap and productivity demands, as smart factories leverage these technologies for efficient and sustainable operations. Many manufacturers plan substantial investments in digital transformation to remain competitive and build a more resilient workforce.
Just in time, a generation of tech-savvy workers, Generation Z, is now entering the workforce. Although this might seem like an ideal opportunity to fill manufacturing roles, few Gen Z applicants are applying, and even those hired frequently leave soon after. This trend raises an essential question: What are Gen Z workers really seeking in a manufacturing career?
What Gen Z can bring to the table
Born between 1997 and 2012, Generation Z is digitally fluent, having grown up with smartphones and the internet. They are socially aware and environmentally conscious, facing unique challenges like missing face-to-face events during the pandemic and adjusting to virtual learning.
These traits make Gen Z well-suited for careers in manufacturing, where their tech skills and innovative mindset can drive efficiency and support sustainable practices. Their adaptability and awareness position them as valuable contributors to industrial manufacturing solutions.
-
Digital intuition
Generation Z is the first generation to grow up entirely in the digital age, with their formative years shaped by the internet and the pandemic. Technologically savvy, these workers bring a unique perspective to engineering capabilities and improving operational efficiency, viewing advancements with excitement. In fact, a study found that 48% of Gen Z respondents felt optimistic about automation's impact on the manufacturing industry.
-
Excellent skills match
Generation Z is entering the workforce at a time when there is an extraordinary demand for digital skills. In the past five years, The demand for manufacturing careers has surged by 75% and is expected to keep growing as emerging technologies like virtual reality (VR) and augmented reality (AR) reshape the industry. Gen Z's inherent inclination towards these fields positions them as valuable assets in boosting tech-driven manufacturing capabilities.
-
Better workplace culture
Gen Z's technological expertise is just one of their many strengths. This generation is also notably ethical and value-oriented, with 50% indicating they would decline a job if an employer's values don't match their own. Interestingly, this generation prioritizes other factors over compensation, being the only demographic to rank career advancement and meaningful work above salary. This suggests that they can help build a work culture that highlights social values and job satisfaction—worthwhile trends that global manufacturing companies can adopt.
-
Improved workplace safety
Gen Z employees are recognized for their strong awareness of risks and safety protocols, making them some of the most vigilant members of the labor force. For engineering manufacturers aiming to comply with intensified enforcement guidelines and rising penalties, these Gen Z workers could be invaluable assets.
8 ways to entice Gen Z to take on manufacturing jobs or careers
Manufacturing is struggling to find enough workers to meet demand, with high turnover rates. Attracting replacements is crucial for the industry's sustainability, but retaining Gen Z workers in manufacturing roles is challenging. Here are some strategies employers can use to engage and keep them:
-
Think beyond the salary.
Work-life balance components like flexible schedules, remote work options, and promoting mental health initiatives can create a supportive environment. While competitive pay is important, high pay isn't a top concern for Gen Z. By highlighting well-being, employers can enhance employee retention and loyalty among the younger workers in the industry.
-
Invest in your workers.
It helps to view Gen Z workers as valuable investments rather than mere expenses. Some companies successfully implement this approach by revamping their employee management frameworks to provide greater adaptability and empower workers in shaping their career paths. For example, implementing mentorship programs can enhance professional development and engagement among younger employees.
-
Prioritize people instead of machines.
Gen Z appreciates compassionate leadership, which manufacturers can support by restructuring schedules. The usual practice was to let manufacturing workers go on 12-hour shifts to ensure the optimum function of machines 24 hours daily. Instead, companies can offer part-time roles, enabling workers to choose their hours.
-
Improve corporate branding.
Because Gen Z values meaningful work, companies can showcase their commitment to social responsibility by supporting local communities and environmental sustainability initiatives. For example, a manufacturer might highlight eco-friendly practices or employee volunteer programs, fostering a sense of purpose that resonates with younger workers.
-
Offer problem-solving opportunities
Gen Z are known for being adept problem-solvers. Give them tasks that need critical thinking, like improving processes or joining team projects. This not only keeps them engaged but also helps them develop important people skills, addressing the issue of their lack of experience in this area.
-
Help them build resilient skills.
Try transforming traditional roles in manufacturing to enhance career development and employee retention. For instance, you can encourage employees to transition from assembly line workers to quality assurance coordinators. By providing training in quality control techniques and problem-solving, employers can empower these workers to improve product standards and grow their career.
-
Foster a collaborative culture.
Create an environment that encourages teamwork and open communication. Implementing regular team-building activities and brainstorming sessions allows Gen Z workers to share ideas and collaborate on projects. This sense of community not only boosts morale but also enhances innovation, making employees feel valued and connected to their workplace.
-
Emphasize continuous learning.
Foster a culture of lifelong learning by providing regular training and development opportunities.
Providing access to online courses, workshops, or industry conferences allows Gen Z employees to enhance their skills and stay current with industry trends. This investment in their growth shows commitment to their professional development and future success.In conclusion, attracting Gen Z to manufacturing is crucial for the industry's future, as their fresh perspectives, technological savvy, and desire for meaningful work can drive innovation. They can also boost productivity and ensure a sustainable workforce in an increasingly competitive landscape.
As one of the Top 20 EMS companies in the world, IMI has over 40 years of experience in providing electronics manufacturing and technology solutions.
We are ready to support your business on a global scale.
Our proven technical expertise, worldwide reach, and vast experience in high-growth and emerging markets make us the ideal global manufacturing solutions partner.
Let's work together to build our future today.
Other Blog
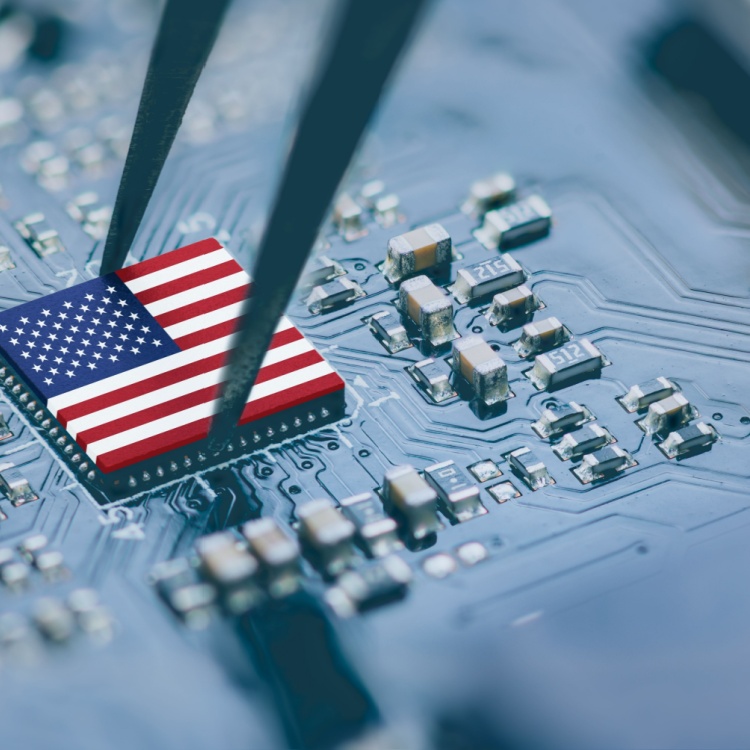
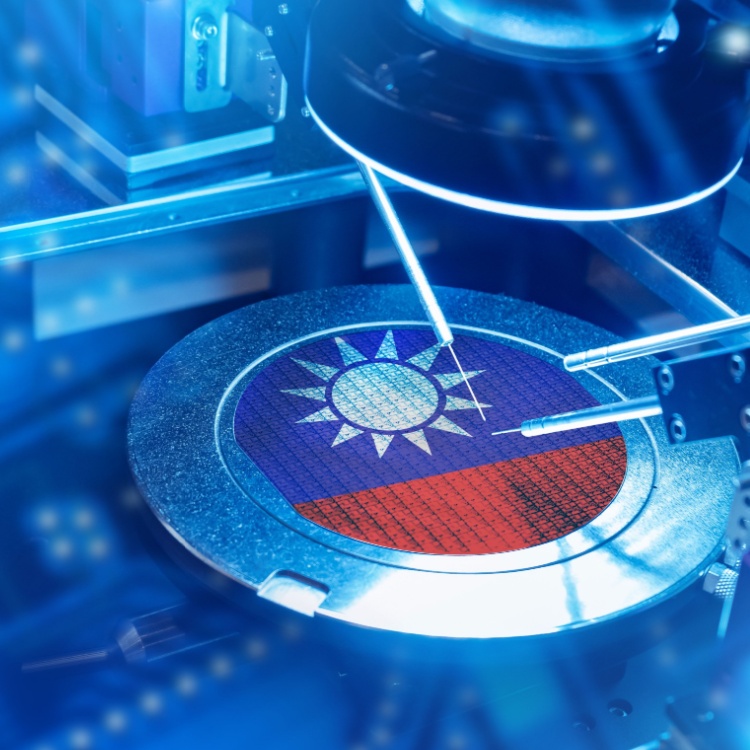
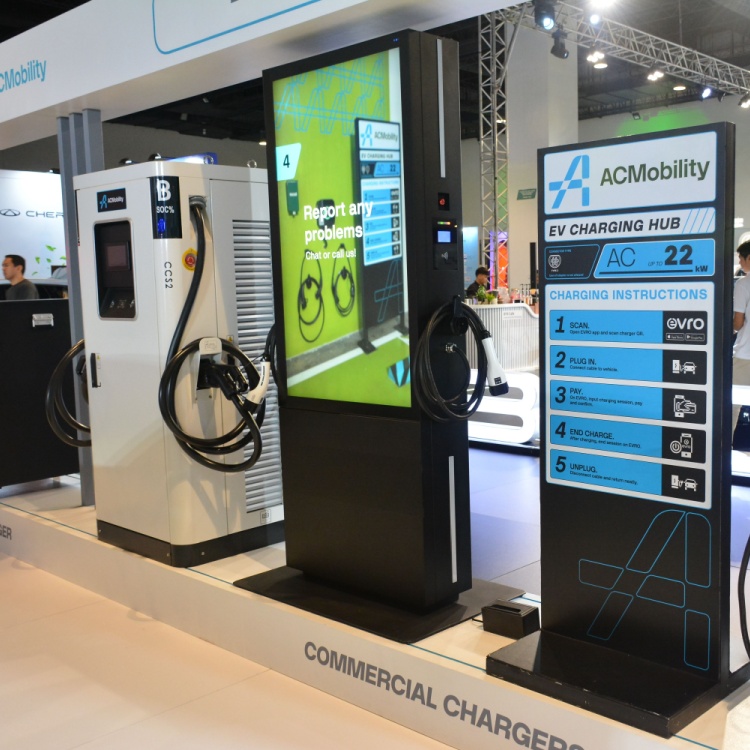