Earth-Friendly Electronics: A Work in Progress
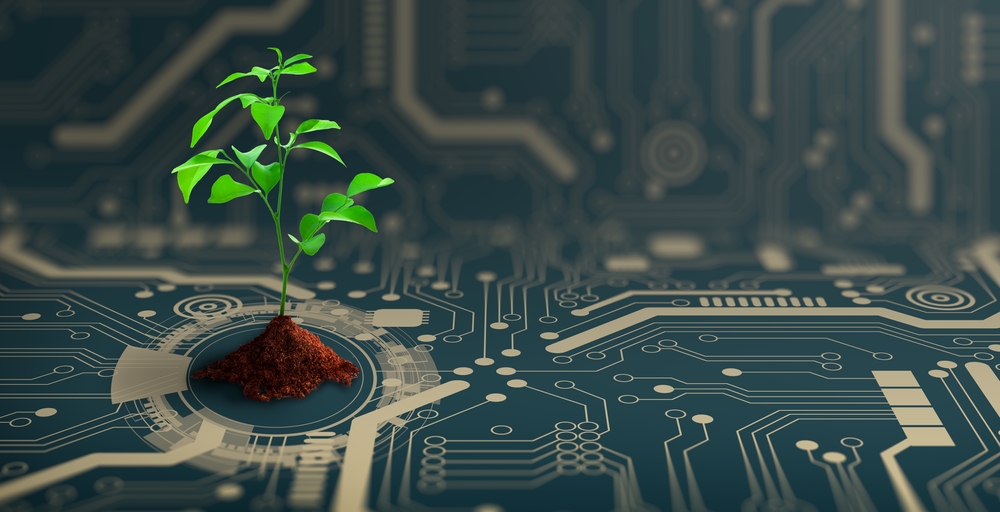
Can electronics manufacturing go green? Scientists and researchers are turning to both natural and synthetic materials to find a way.
Technology is paving the way for productivity and innovation in various industries while enabling progress in our society. Gadgets do make life easier, but our digital lifestyle has also made electronic waste the world’s fastest-growing domestic stream.
Technology is fueling our future, but it is also putting us in peril. How can we drastically lessen the environmental impact of electronics?
Engineering for sustainability
A circuit board can be disposed of by dissolving it in water. High-performance materials are given a new lease in life. Algae-infused ink is used for 3D printing. Scientists, engineers, and researchers are working hard to develop sustainable electronics for a greener future.
To commemorate Earth Day, the University of Washington showcased three projects aimed at designing sustainable electronics without sacrificing performance. Let’s take a look.
Designing a sustainable computer mouse
Vikram Iyer, assistant professor in the Paul G. Allen School of Computer Science & Engineering, Bichlien Nguyen, a principal researcher at Microsoft, and Vicente Arroyos, a University of Washington doctoral student in the Allen School, have built a working prototype of a sustainable computer mouse.
Since the chipmaking process accounts for around 80% of carbon emissions in electronics manufacturing, the team optimized their circuit design to use the fewest silicon chips possible. The computer mouse has a biodegradable circuit board made of flax fibers, while the case was 3D-printed using compostable materials such as polylactic acid (PLA) or polyvinyl alcohol (PVA). The circuit board and mouse case can be disposed of by dissolving them in water.
“When we submerge our circuit board in water, the fibers start to come apart and the whole thing just disintegrates. This takes about five to 10 minutes in hot water, or a few hours at room temperature,” Iyer explained. “After this, we’re left with the chips and circuit traces which we can filter out. We also designed two different cases, one of these can dissolve in water and the other can be commercially composted.”
To evaluate their prototype’s environmental impact, the team compared the life cycle assessment of a conventional mouse design with theirs. The team discovered that their prototype significantly reduces e-waste and carbon footprint. Their design also makes component reclamation and reuse easier.
Going natural with sustainable alternatives to plastics
“Our group focuses on developing materials derived from biological matter. In addition to seaweeds and other forms of algae, this includes plant residues and microbial products,” Eleftheria Roumeli, an assistant professor of materials science and engineering and researcher at the Molecular Engineering & Sciences Institute, explained.
The Roumeli Research Group studies biological materials, such as plant & algae cells and tissues, to develop biodegradable plastics. The group recently published a paper on 3D printing inks developed from spirulina cells, a type of blue-green algae, and varying amounts of cellulose fibers.
“Cellulose is the most abundant natural polymer, and these inks are 100% compostable in soil,” Roumeli shared. “There’s no special composting facility required!”
Healing carbon-fiber composites with heat
Lightweight and strong, carbon fiber materials are used in high-performance products like sporting goods, race cars, and airplanes. Unfortunately, the very strength of carbon fiber also means it is difficult to recycle.
Together with his team, Aniruddh Vashisth, an assistant professor of mechanical engineering at the University of Washington, has created a new type of carbon-fiber-reinforced material that is just as strong and light as its predecessor but can heal itself–it just needs a little help from heat.
"Developing fatigue-resistant composites is a major need in the manufacturing community," Vashisth shared. "In this paper, we demonstrate a material where either traditional heat sources or radio frequency heating can be used to reverse and postpone its aging process indefinitely."
The focus of Vashisth’s team is on synthetic polymers that can be recycled and reprocessed many times over.
“Unlike other plastics, these materials do not lose their thermo-mechanical properties during reprocessing and recycling. This is exciting since you can reuse the same material again and again!” Vashisth said. “This phenomenon of retaining material properties is possible because the building blocks that make up these materials can detach and reattach, just like Legos. So when we are recycling, we are disassembling and reassembling the Legos.”
As one of the Top 19 EMS companies in the world, IMI has over 40 years of experience in providing electronics manufacturing and technology solutions.
We are ready to support your business on a global scale.
Our proven technical expertise, worldwide reach, and vast experience in high-growth and emerging markets make us the ideal global manufacturing solutions partner.
Let's work together to build our future today.