COVID-19 and the Future of Electronics Manufacturing
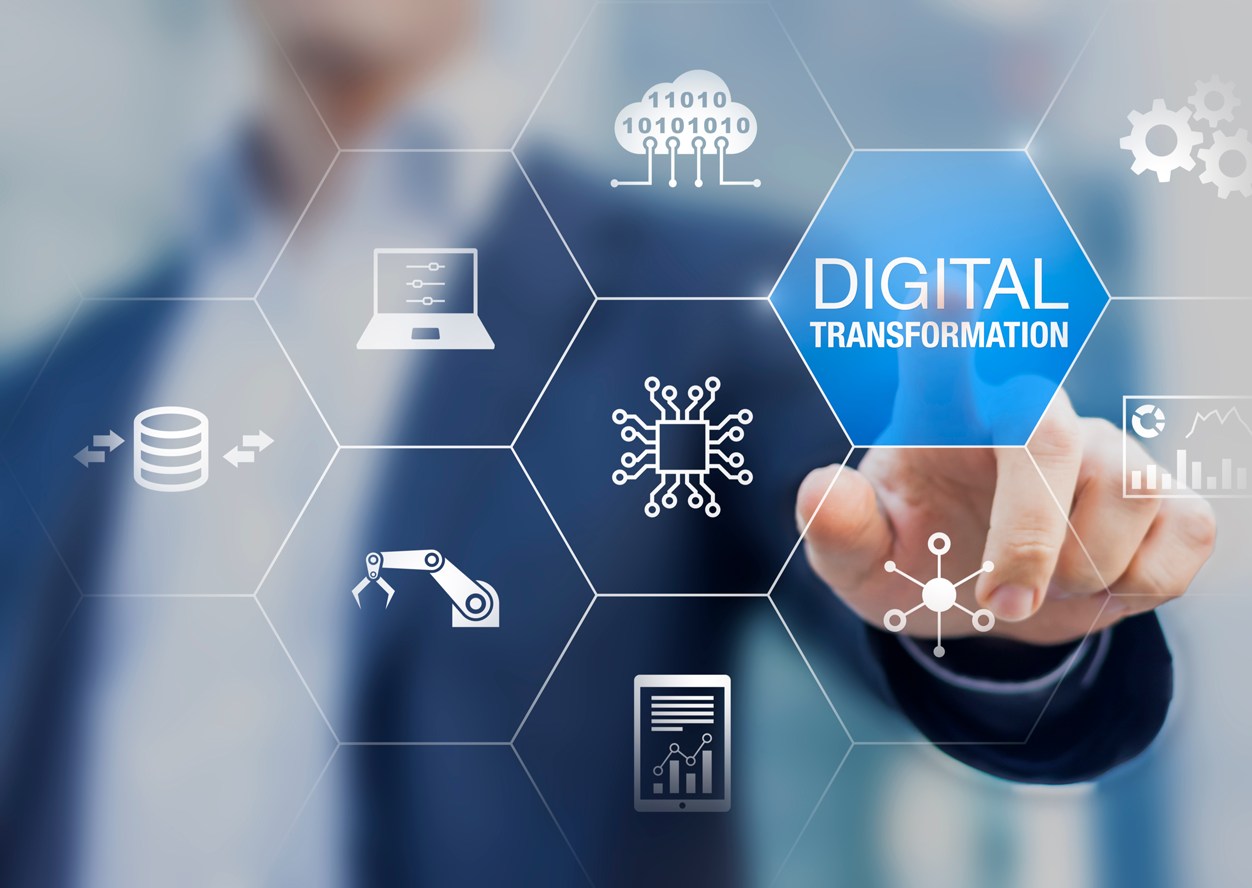
As it disrupts businesses and industries worldwide, the COVID-19 pandemic shows how a digital transformation may be key to the survival—and success—of electronics manufacturing companies.
“For the first time in modern manufacturing history, demand, supply, and workforce availability are affected globally at the same time,” says Artem Kroupenev, Vice- President of Strategy at Augury, a technology company based in the United States and Israel.
It is a sobering, unprecedented reality, and one that has thrown businesses around the world into a situation of uncertainty. For the manufacturing industry, the COVID-19 pandemic is affecting workplace health and safety, disrupting supply chains, and bringing production lines to a standstill. How can electronics manufacturing companies survive—and thrive—in this new normal? What strategies should they formulate and what capabilities should they acquire to operate in this uncharted territory?
Harnessing the power of Industry 4.0
We have seen how this global health crisis has caused a seismic shift in the way we live and work. Companies are utilizing remote-working tools. Luxury brands are making personal protective equipment (PPE) and distilleries are producing hand sanitizers. Online groceries are flourishing and museums around the world are offering virtual tours. From e-commerce and a flexible workplace to telemedicine and a shift in production, the COVID-19 pandemic has pushed companies to operate in new ways.
For the electronics manufacturing industry, the challenges of distance and disruption underscore the importance of digital transformation to keep a company flexible and resilient during these uncertain times. Certain Industry 4.0 capabilities can address the issues that these companies face, as enumerated by McKinsey:
- Data, computational power and connectivity (sensors, the Internet of Things or IoT, cloud technology and blockchain)
- Analytics and intelligence (Big Data, advanced analytics, artificial intelligence or AI, and knowledge-work automation)
- Human-machine interaction (virtual reality, augmented reality, robotics, automation, robotic process automation or RPA, and chatbots)
- Advanced production methods (additive manufacturing and renewable energy)
Plants, machines, equipment, and other vital components can be equipped with sensors capable of conveying vast amounts of data through the Industrial Internet of Things (IIoT). “By aggregating their data in the cloud, companies get real-time data for remote oversight, aggregated and comparative intelligence across global factories, suppliers, and business units, and the ability to leverage technologies to solve pressing problems,” says Anna-Katrina Shedletsky, CEO and Founder of Instrumental.
Since electronics manufacturing is a highly manual process, the need for physical distancing in production lines poses another challenge, making a stronger argument for investing in automation. “While manufacturers may initially be hesitant to take on large capital intensive projects like automation right now, the payoffs of a workforce that doesn’t take breaks and doesn’t get sick will be appealing to those with strong capital positions—enabling acceleration in efficiency during this time that will cut costs and boost bottom lines,” shares Shedletsky.
According to research by McKinsey, companies that are transitioning to digital manufacturing have experienced “30 to 50 percent reductions of machine downtime, 15 to 30 percent improvements in labor productivity, 10 to 30 percent increases in throughput, and 10 to 20 percent decreases in the cost of quality.”
“These breakthroughs create impact across the value chain that may be even more important, if harder to measure: increased flexibility to meet customer demand, faster speed to market, and better integration within the supply chain,” says McKinsey.
Five principles for your digital transformation
For a manufacturer to effectively scale digital manufacturing across its global network, its transformation must be based on five principles, as outlined by McKinsey:
- Focus on business value. Digital transformation must come from the company’s digital strategy, with well-defined financial and operational-performance objectives. Where and how can digital manufacturing support real business needs? Which digital solutions should the company prioritize, in light of the investment required, as well as the level of readiness of its data and technology infrastructure?
- Have an integrated approach. A company should work closely with IT to establish the data and technical architecture. As it invests in and develops new roles, it should reskill and upskill its existing workforce. It should also follow an agile way of working—building “minimum viable products rapidly and iteratively while keeping things simple and learning along the way to make adjustments as needed.”
- Create capabilities for deployment. A community of practitioners (digital change agents, data engineers, IT architects, and data scientists) should be established to assist leadership and the front line upon implementation. There should also be “translators” during exchanges between technical and business staff.
- Scale deployment, capabilities, and technology. Strong governance of innovation through a certain degree of centralization should be established: insights developed from this innovation hub can then be replicated across the business. Clear objectives, guidelines on how to drive development and scaling, as well as positive collaboration are important. According to McKinsey, there should be a roadmap for the scale-up across the network, with adapted deployment models that “best fit the organization’s context and needs, scaling mechanisms, and resourcing strategy.” The sequence and timeline of scaling should account for business needs, value at stake, potential ROI, and site readiness.
- Building for the future. The company should establish a flexible technology architecture to meet its future needs. By taking a long-term view, it will be able to sustain its new architecture by anticipating potential developments and disruptions.
Is your company ready for a digital manufacturing transformation?
To assess your company’s readiness for digital manufacturing transformation, McKinsey says leaders should consider the following questions:
- Where would digital, robotics, and advanced analytics create the most value in your manufacturing network?
- What is your current ambition level for a digital transformation? What impact do you aspire to in the short term and medium term, respectively?
- How have you connected your digital strategy to your existing operations strategy?
- How advanced is your organization in its journey from digital development and piloting to at-scale deployment?
- Have you already established a team within your organization to support robust governance?
- What successes have you achieved? Which factors have been critical to success?
- What main challenges are you facing? What mitigation actions are you working on?
- How are you balancing the need for tangible change with the imperative for a quick return on investment?
- To what extent are you combining transformations of your business, technology, and organizational capabilities?
This global health crisis has pushed individuals, businesses, and industries alike to adapt to a new normal. Despite all the negative effects of this pandemic—on lives and economies, healthcare systems and mental health—that push to adapt and adjust is the silver lining. And those who are quick to respond to these changes, who transform and become more flexible and resilient, will be the ones in a better position to succeed and excel when this crisis comes to pass.
Other Blog
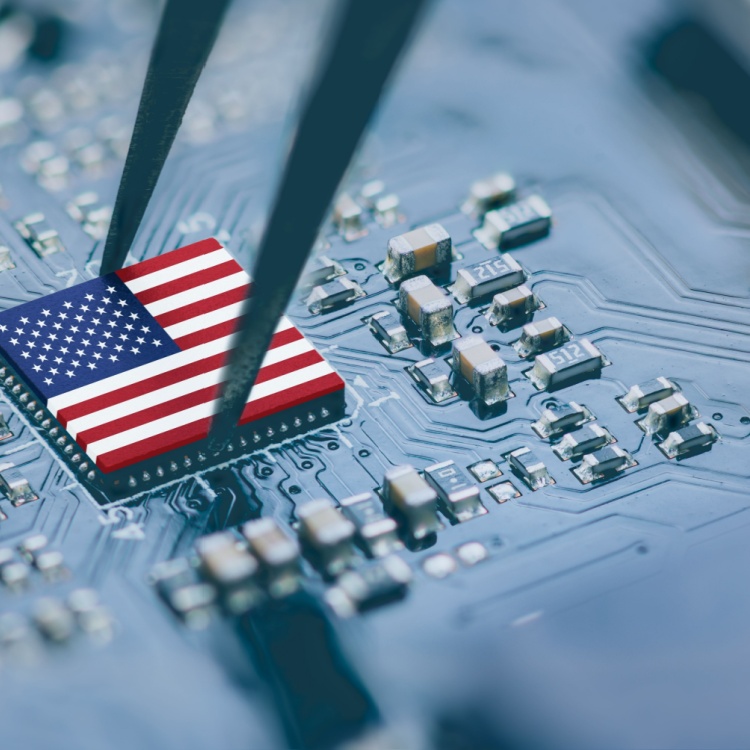
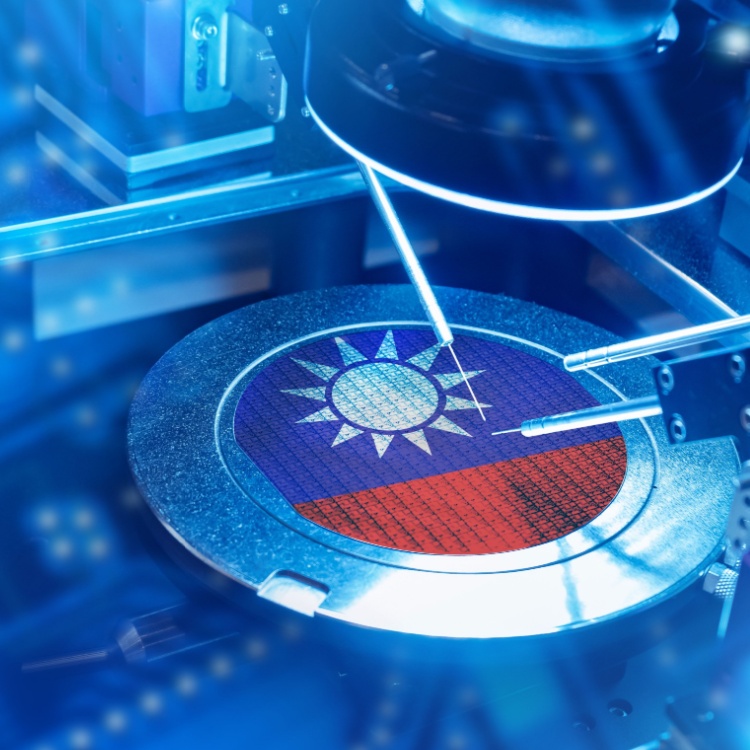
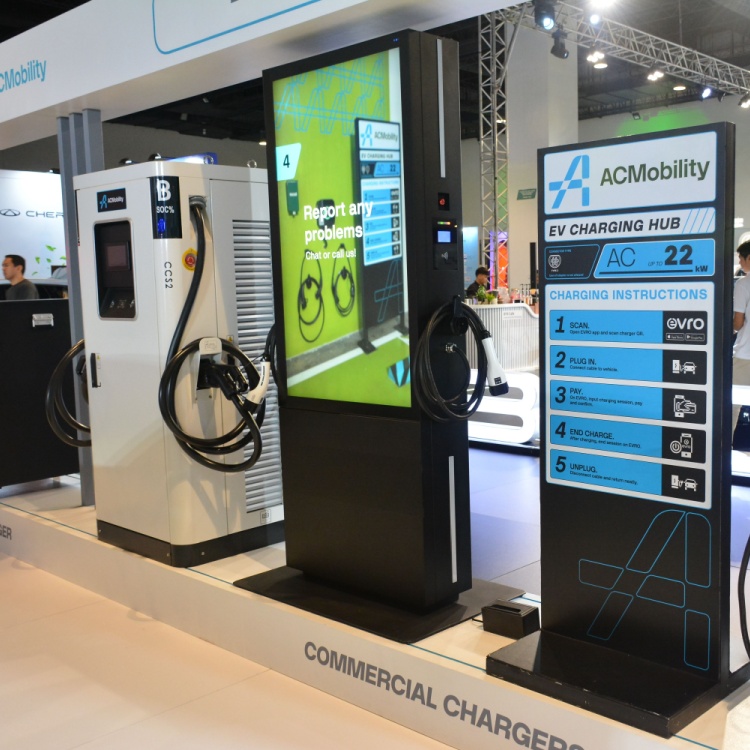