Collaboration and Engineering in Our New Normal
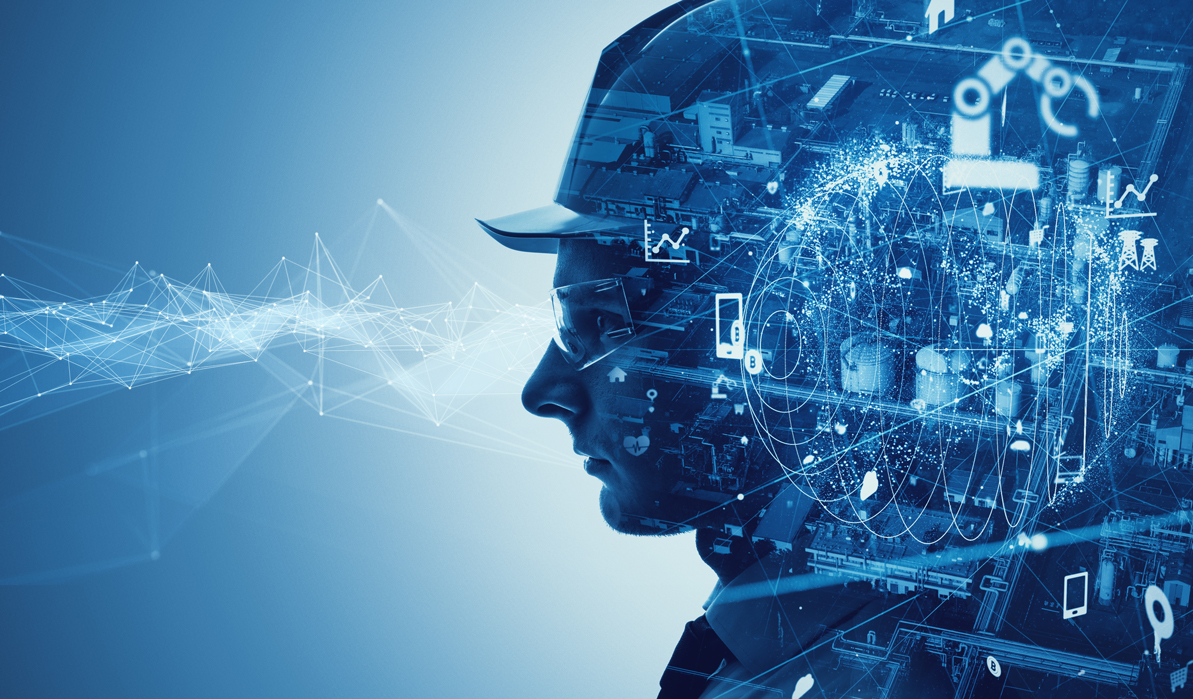
How are engineers around the world staying productive and efficient amid the challenges and constraints brought about by the pandemic?
Designing, building, and testing complex products require a high level of collaboration, computing power, and face-to-face interaction. Because of the pandemic, this has become challenging for engineers around the world.
“Being able to engage directly with another nearby designer and ask ‘what do you think about this’ can make the difference between spending an hour or a day to resolve a challenging issue,” Thomas Fowler, vice president of engineering, Silicon Labs, shared with EE Times Asia.
As COVID-19 changes the way we live and work, engineers are turning to digital tools and the Internet of Things (IoT) to sustain their productivity amid the pandemic.
Cloud-based design tools
Engineers require high computational power and graphics-heavy computer-aided design (CAD) software to accomplish their tasks.
Because of this, simulation and visualization design tools are normally used by engineers on-premises. Many engineering organizations have delayed shifting to a cloud-based model because of privacy and security concerns for intellectual property.
The pandemic has changed that mindset, with the usage of and demand for cloud-based design tools and remote collaboration platforms rising.
“We’re definitely seeing increased interest and usage at a professional level,” said David Katzman, Head of Customer Experience and Strategy for Onshape, a cloud-based CAD platform.
“People are just starting to wrap their head around this so it takes some time,” Katzman told Digital Engineering.
Specializing in product development, mechanical engineer Kay Yang has accelerated her use of digital design tools because of the pandemic. She sees digital adoption happening more quickly in the design and prototyping of a product. “We’re in Los Angeles, so we can’t physically meet and evaluate a prototype together, so we evaluate things digitally,” Yang shared with The American Society of Mechanical Engineers (ASME). When physical prototypes are required, Yang’s team makes a 3D-printing file of the prototype.
Outsourcing prototypes is a convenient option for engineers, with many companies capable of building a prototype from a CAD design and shipping it to the customer. Jonah Myerberg, Chief Technology Officer of Desktop Metal, shared with the ASME that his team launched a website that “prints 3D metal components for mission-critical COVID-19 applications for free.”
The Internet of Things for product evaluation and monitoring
While the use of IoT in product development is not new, the engineering industry has been slow to adopt the technology, says Anna-Katrina Shedletsky, chief executive officer at Instrumental Inc.
With physical distancing and lockdown measures making remote work our new reality, that way of thinking may change in order to sustain product development and equipment maintenance.
To minimize the need for on-site engineers during the build process, Instrumental Inc. places IoT sensors and other instruments to capture product data and record images. The information can then be accessed by the company in the cloud, on a file transfer protocol (FTP) server, or at the company’s local site.
Recounting a build event for a tech company, Shedletsky says that IoT sensors enabled an engineer based in Chicago to spot a tooling issue during a build event in China—saving the company significant amounts of money, time, and resources.
Industrial assets are also being connected and streaming information to the cloud, according to Oliver Pauzet, vice-president of product and IoT solutions for Sierra Wireless.
“IoT and digitization are not new, but I will say COVID-19 has accelerated that trend,” Pauzet told the ASME. “It’s making a lot of equipment manufacturers realize they need that connection. In the past, they could go into the field to check on their industrial assets or perform regularly scheduled maintenance.”
Real-time feedback from sensors and other instruments in the field enables manufacturers to collect important data and identify—even anticipate—equipment failure.
“Rather than sending someone out in the field to fix a nonworking asset, they can see the digital twin of each of their assets operating in the cloud and detect if something is going to go wrong,” Pauzet said. “Without IoT, they have no view at all. They just have to wait to get a call saying something doesn’t work.”
Embracing the downtime
Working from home may be the perfect opportunity to step back and evaluate how you do your job—to streamline your process or be more thoughtful and deliberate in your approach. Slowing down could lead you to your next bright idea.
“Instead of rushing to create a prototype, I’m now spending more time taking a research perspective, and looking at different ways we might approach a particular design,” Matt Kuhn, a project leader at the Center for Device Innovation (CDI) in Houston, Texas, shared with the ASME.
“You never know where innovation is going to come from—or who it is going to come from,” Myerberg of Desktop Metal said. “But, as engineers, we’re used to working within certain constraints. We always find a way to figure it out. There’s no reason why we can’t figure it out in this situation, too.”
This combination of downtime and digital tools could be a winning combination that unlocks a new wave of innovation in engineering.
As one of the Top 20 EMS companies in the world, IMI has over 40 years of experience in providing electronics manufacturing and technology solutions.
At IMI, we believe that humanity drives technology, and we direct our passion at solutions that enhance our way of living. With more than 400,000 square meters of factory space in 22 factories across 10 countries, we are positioned to build your business on a global scale.
Our proven technical expertise, worldwide reach, and vast experience in high-growth and emerging markets make us the ideal global manufacturing solutions partner.
Let's work together to build our future today.
Other Blog
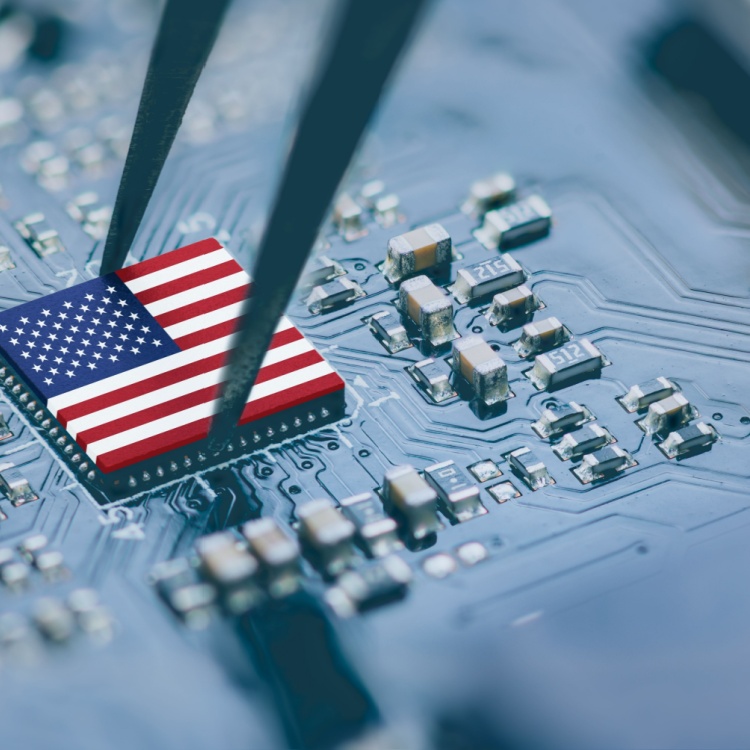
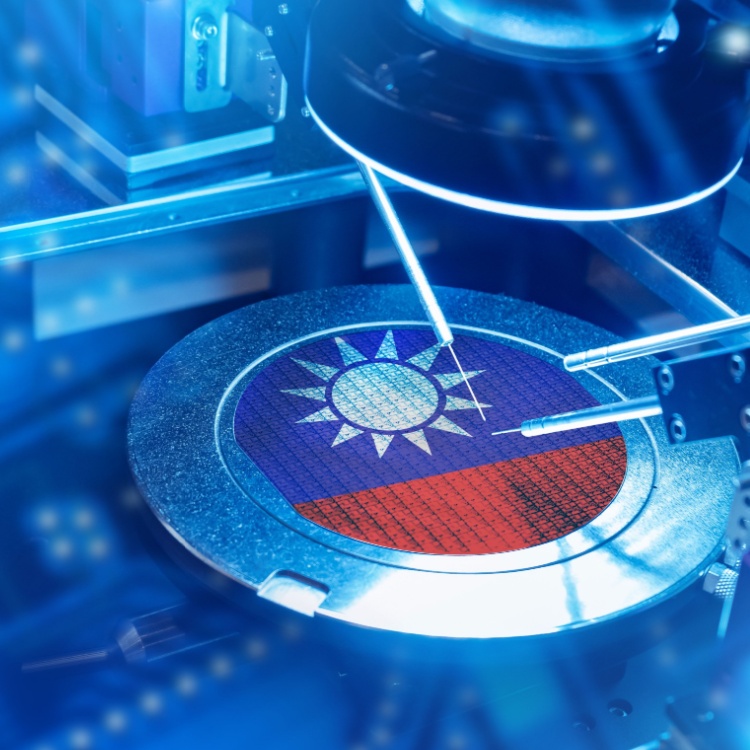
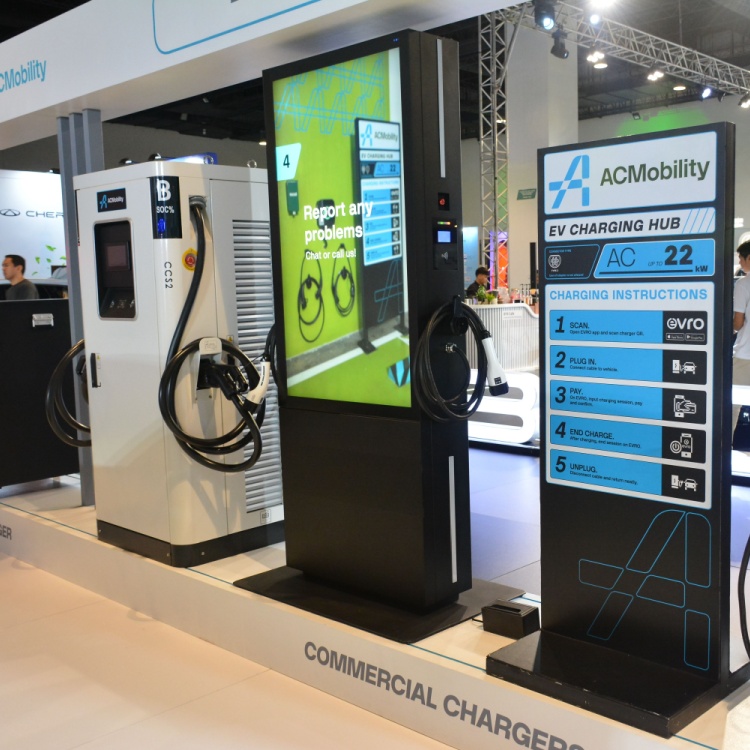